Knotting mould for crucible and knotting method
A mold and crucible technology is applied in the field of crucible knotting molds and knotting, which can solve the problems of losing the quality of metallurgical ingots without considering the removal of water vapor, and the quality of the sintered inner wall is bad, so as to improve the quality, eliminate defects and hidden dangers, The effect of preventing transverse cracks in the crucible
- Summary
- Abstract
- Description
- Claims
- Application Information
AI Technical Summary
Problems solved by technology
Method used
Image
Examples
Embodiment Construction
[0027] The present invention will be described in further detail below in conjunction with the accompanying drawings and embodiments.
[0028] A crucible knotting mould, comprising an inner ring mold 4 and an outer ring mold 3, a furnace body wall 8 is arranged outside the inner ring mold 4, an outer ring mold 3 is arranged between the inner ring mold 4 and the furnace body wall 8, The space between the furnace body wall 8 and the inner ring mold 4 is filled with magnesium oxide dry shot 1 5; the space between the inner ring mold 4 and the outer ring mold 3 is filled with magnesium oxide dry shot 2 6; the outer ring The cavity between the mold 3 and the furnace body wall 8 is filled with a mixed dry hammering material 7 .
[0029] The outer ring mold 3 is a ring-shaped mold, the height of the outer ring mold 3 is one-third of the height of the inner ring mold 4, and the outer ring mold 3 is set at the outer top third of the inner ring mold 4. position, the outer ring mold 3 c...
PUM
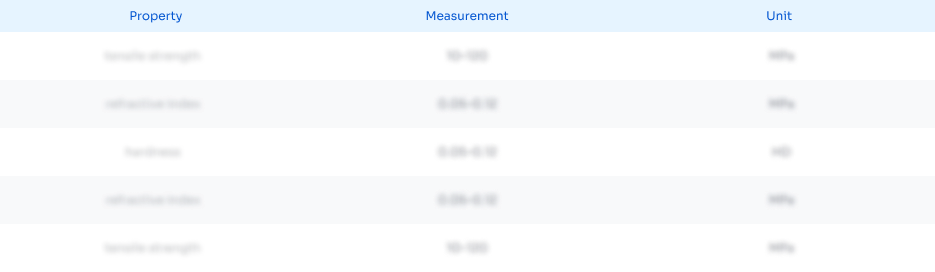
Abstract
Description
Claims
Application Information

- R&D
- Intellectual Property
- Life Sciences
- Materials
- Tech Scout
- Unparalleled Data Quality
- Higher Quality Content
- 60% Fewer Hallucinations
Browse by: Latest US Patents, China's latest patents, Technical Efficacy Thesaurus, Application Domain, Technology Topic, Popular Technical Reports.
© 2025 PatSnap. All rights reserved.Legal|Privacy policy|Modern Slavery Act Transparency Statement|Sitemap|About US| Contact US: help@patsnap.com