Boiler water high-utilization-rate method
A technology of utilization rate and furnace water, applied in the field of furnace water recycling in the glass hardening process, can solve the problems of limited furnace water life, low efficiency, affecting production efficiency, etc.
- Summary
- Abstract
- Description
- Claims
- Application Information
AI Technical Summary
Problems solved by technology
Method used
Image
Examples
Embodiment Construction
[0021] The specific embodiments of the present invention will be further described below in conjunction with the accompanying drawings. It should be noted here that the description of the following embodiments is used to help understand the invention, but does not constitute a limitation to the invention.
[0022] figure 1 , figure 2 A method for high utilization rate of boiler water disclosed by the present invention is shown, comprising the following steps:
[0023] (1) Put the collection basin into the bottom of high temperature furnace 1;
[0024] (2) Add anhydrous trisodium phosphate in a ratio of 3‰-8‰ into the high temperature furnace 1;
[0025] (3) Raise the temperature in the high-temperature furnace 1 to 400-500°C for processing;
[0026] (4) Take out the collection basin 2 and cool the collected sediment to freeze, then put the collection basin 2 back to the bottom of the high temperature furnace 1 .
[0027] As a preferred solution of the present invention, ...
PUM
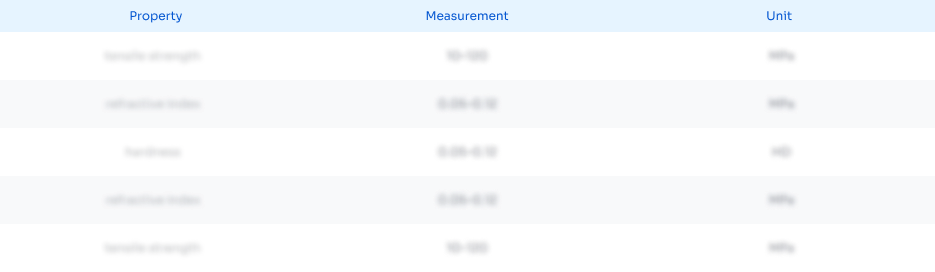
Abstract
Description
Claims
Application Information

- R&D
- Intellectual Property
- Life Sciences
- Materials
- Tech Scout
- Unparalleled Data Quality
- Higher Quality Content
- 60% Fewer Hallucinations
Browse by: Latest US Patents, China's latest patents, Technical Efficacy Thesaurus, Application Domain, Technology Topic, Popular Technical Reports.
© 2025 PatSnap. All rights reserved.Legal|Privacy policy|Modern Slavery Act Transparency Statement|Sitemap|About US| Contact US: help@patsnap.com