High-precision punch forming die for ceiling crossbeam in bullet train carriage
A technology of stamping and forming inside the carriage, which is applied in the field of high-precision stamping and forming moulds for the ceiling beams in the carriage of the motor train, which can solve the problems of no precise positioning, no fixing function, no auxiliary pick-up and so on.
- Summary
- Abstract
- Description
- Claims
- Application Information
AI Technical Summary
Problems solved by technology
Method used
Image
Examples
Embodiment 1
[0027] Example 1: See Figure 1-4 , a high-precision stamping and forming mold for the ceiling beam in the motor car compartment, including a bottom plate 15, and also includes an ejection structure 8 that is convenient for taking parts, a fixing structure 9 that prevents the workpiece from shifting, and a positioning structure that ensures the normal operation of the device;
[0028] The both sides of base plate 15 tops are all provided with two supporting feet 16, and the top of supporting feet 16 is provided with support plate 14, and the top middle position of support plate 14 is equipped with lower mold base 18, and the supporting plate of lower mold base 18 both sides A side plate 19 is installed on the top of 14, and an empty slot 17 is provided at the central position of the bottom end of the support plate 14, and the ejection structure 8 is arranged inside the empty slot 17;
[0029] The top of the support plate 14 on one side of the side plate 19 is provided with two...
Embodiment 2
[0034] Embodiment 2: The ejector structure 8 includes a first cylinder 801, a push rod 802, an auxiliary spring 803 and a horizontal plate 804. The first cylinder 801 is arranged at the top center of the bottom plate 15. The model of the first cylinder 801 can be SC63 , and the top of the first cylinder 801 extends to the inside of the cavity 17, a horizontal plate 804 is arranged horizontally inside the cavity 17 above the first cylinder 801, and both sides of the top of the horizontal plate 804 are provided with push rods 802, the cavity The outer wall of the push rod 802 between 17 and the horizontal plate 804 is provided with an auxiliary spring 803, and the top and bottom ends of the auxiliary spring 803 are welded to the hollow groove 17 and the horizontal plate 804 respectively;
[0035] The top ends of the ejector pins 802 all extend to the top of the support plate 14, and the ejector pins 802 are all arranged between the lower mold base 18 and the side plate 19;
[00...
Embodiment 3
[0037] Embodiment 3: The fixed structure 9 includes an extension rod 901, a fixed seat 902, a buffer spring 903 and a pressing plate 904. The fixed seat 902 is arranged at the bottom of the top plate 13 on both sides of the upper mold base 12, and the bottom of the fixed seat 902 is provided with Extension rod 901, the bottom end of extension rod 901 is equipped with pressing plate 904, and the outer wall of extension rod 901 between pressing plate 904 and fixed seat 902 is all sleeved with buffer spring 903, and the top and bottom end of buffer spring 903 are connected with the fixed seat respectively. 902 and pressing plate 904 are welded;
[0038] The top end of the extension rod 901 runs through the inside of the fixing seat 902 and the top plate 13, and the top end of the extension rod 901 extends to the top of the top plate 13;
[0039] Specifically, such as figure 1 , figure 2 and image 3 As shown, when using this mechanism, the pressing plate 904 is displaced down...
PUM
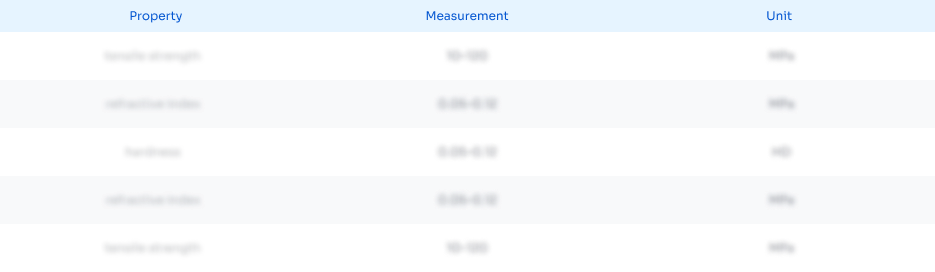
Abstract
Description
Claims
Application Information

- R&D
- Intellectual Property
- Life Sciences
- Materials
- Tech Scout
- Unparalleled Data Quality
- Higher Quality Content
- 60% Fewer Hallucinations
Browse by: Latest US Patents, China's latest patents, Technical Efficacy Thesaurus, Application Domain, Technology Topic, Popular Technical Reports.
© 2025 PatSnap. All rights reserved.Legal|Privacy policy|Modern Slavery Act Transparency Statement|Sitemap|About US| Contact US: help@patsnap.com