Porous polyurethane scaffold based on 3D printing
A 3D printing and polyurethane technology, applied in the field of 3D printing, can solve problems such as difficult separation, increased operation process, and inability to accurately control the degradation rate.
- Summary
- Abstract
- Description
- Claims
- Application Information
AI Technical Summary
Problems solved by technology
Method used
Examples
Embodiment Construction
[0018] A porous polyurethane scaffold based on 3D printing, which is formed by rapid prototyping technology from β-TCP powder and polyurethane particles.
[0019] Follow the steps below:
[0020] (1) Build a polyurethane / β-TCP additive manufacturing system;
[0021] (2) Preparation of polyurethane / β-TCP support printing consumables;
[0022] (3) 3D printed porous polyurethane scaffold.
[0023] Step (2): Improve the dispersion of β-tricalcium phosphate by modifying the surface of β-TCP; blend β-TCP powder and polyurethane particles in a mixer in a certain ratio (1:1) to prepare Produce polyurethane / β-TCP printing consumables.
[0024] A kind of purposes of porous polyurethane support:
[0025] The porous polyurethane scaffold is used as a human auricle morphology scaffold.
[0026] The preparation method of the porous polyurethane stent is based on the three-dimensional CT scanning technology of the skull to perform three-dimensional craniofacial reconstruction, and then ...
PUM
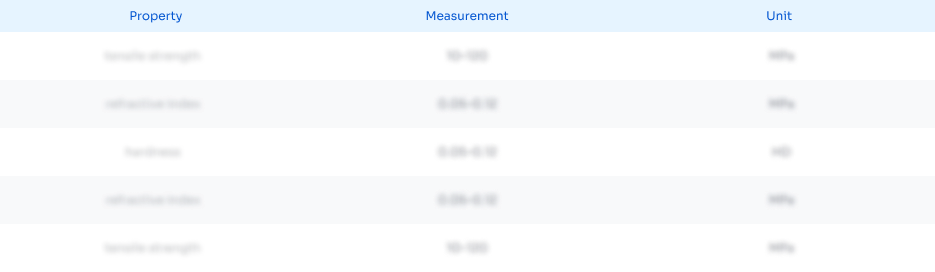
Abstract
Description
Claims
Application Information

- Generate Ideas
- Intellectual Property
- Life Sciences
- Materials
- Tech Scout
- Unparalleled Data Quality
- Higher Quality Content
- 60% Fewer Hallucinations
Browse by: Latest US Patents, China's latest patents, Technical Efficacy Thesaurus, Application Domain, Technology Topic, Popular Technical Reports.
© 2025 PatSnap. All rights reserved.Legal|Privacy policy|Modern Slavery Act Transparency Statement|Sitemap|About US| Contact US: help@patsnap.com