Stator heating method
A heating method and stator technology, applied in the manufacture of motor generators, electrical components, electromechanical devices, etc., can solve the problems of unfilled, poor fluidity, etc., and achieve the effects of improving production efficiency, improving heating efficiency, and prolonging service life
- Summary
- Abstract
- Description
- Claims
- Application Information
AI Technical Summary
Problems solved by technology
Method used
Examples
Embodiment 1
[0029] A stator heating method, the method comprising the steps of:
[0030] (1) Preheating process: first roughen the surface of the stator, then clean and dry the stator to remove the moisture attached to the end of the stator coil, and the stator will be used after preheating. The temperature is 80-100°C, and the heat treatment time is 1h. The preheating method is to arrange a high-frequency induction coil near the coil end of the stator, and then energize the induction coil to perform high-frequency induction heating on the stator, which can make many high-frequency magnetic force lines pass through. Coil ends to enable uniform heating of the stator;
[0031] (2) Resin molding: put the resin material into the extruder, extrude the molten resin through the extruder, add an appropriate amount of diluent to the molten resin, and then use the mold to inject the resin into the coil of the stator The end, and then configure the shielding body for high-frequency induction heatin...
Embodiment 2
[0036] A stator heating method, the method comprising the steps of:
[0037] (1) Preheating process: first roughen the surface of the stator, then clean and dry the stator to remove the moisture attached to the end of the stator coil, and the stator will be used after preheating. The temperature is 80-100°C, and the heat treatment time is 1h. The preheating method is to arrange a high-frequency induction coil near the coil end of the stator, and then energize the induction coil to perform high-frequency induction heating on the stator, which can make many high-frequency magnetic force lines pass through. Coil ends to enable uniform heating of the stator;
[0038] (2) Resin molding: put the resin material into the extruder, extrude the molten resin through the extruder, add an appropriate amount of diluent to the molten resin, and then use the mold to inject the resin into the coil of the stator The end, and then configure the shielding body for high-frequency induction heatin...
Embodiment 3
[0043] A stator heating method, the method comprising the steps of:
[0044] (1) Preheating process: first roughen the surface of the stator, then clean and dry the stator to remove the moisture attached to the end of the stator coil, and the stator will be used after preheating. The temperature is 80-100°C, and the heat treatment time is 1h. The preheating method is to arrange a high-frequency induction coil near the coil end of the stator, and then energize the induction coil to perform high-frequency induction heating on the stator, which can make many high-frequency magnetic force lines pass through. Coil ends to enable uniform heating of the stator;
[0045] (2) Resin molding: put the resin material into the extruder, extrude the molten resin through the extruder, add an appropriate amount of diluent to the molten resin, and then use the mold to inject the resin into the coil of the stator The end, and then configure the shielding body for high-frequency induction heatin...
PUM
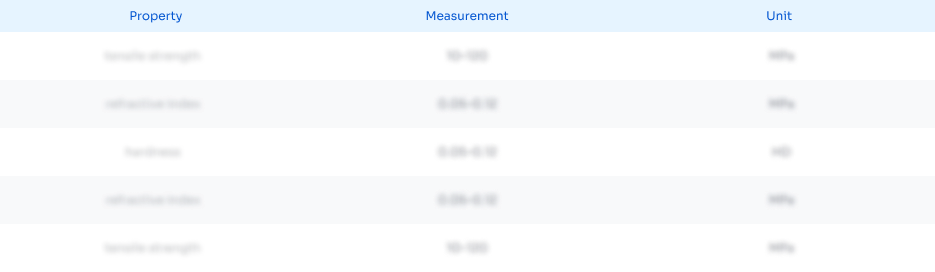
Abstract
Description
Claims
Application Information

- R&D Engineer
- R&D Manager
- IP Professional
- Industry Leading Data Capabilities
- Powerful AI technology
- Patent DNA Extraction
Browse by: Latest US Patents, China's latest patents, Technical Efficacy Thesaurus, Application Domain, Technology Topic, Popular Technical Reports.
© 2024 PatSnap. All rights reserved.Legal|Privacy policy|Modern Slavery Act Transparency Statement|Sitemap|About US| Contact US: help@patsnap.com