Cold-pressed pellet production process
A production process and cold-pressed pelletizing technology, applied in the field of cold-pressed pelletizing production process, can solve the problems of complex manufacturing process, inconvenient management, and low production quality, and achieve the effects of high precision, stable efficiency, and stable sustainability.
- Summary
- Abstract
- Description
- Claims
- Application Information
AI Technical Summary
Problems solved by technology
Method used
Examples
Embodiment 1
[0037] As a preferred embodiment of the cold-pressed pellet production process of the present invention, the manganese content of the ore powder is 36%-40%.
[0038] Mineral powder with a manganese content of 36%-40% is used as an alloy additive to improve the strength, hardness, elastic limit, wear resistance and corrosion resistance of the steel by later pressing; in high alloy steel , It is also used as an austenitic compounding element for refining stainless steel, special alloy steel, stainless steel electrodes, etc.
Embodiment 2
[0040] As a preferred embodiment of the cold-pressed pellet production process of the present invention, the manganese content of dedusting ash is 17%.
[0041] In this embodiment, the dedusting ash is the slag produced after the smelting of the silicon-manganese alloy, and the secondary utilization of the waste material can effectively reduce the cost without affecting the rigidity of the product.
Embodiment 3
[0042] Embodiment 3: As a preferred embodiment of a cold-pressed pellet production process of the present invention, it comprises the following steps:
[0043] Step 1: Select the raw materials of mineral powder and dedusting ash, remove the impurities in the raw materials, and then batch the raw materials according to a certain proportion;
[0044] Step 2: Use the mechanical crushing method to crush and grind the raw materials of mineral powder and dedusting ash for the first time, and then use the ball milling method to carry out secondary crushing on the raw materials, so that the particle fineness of the transported materials can reach the appropriate powder particle fineness for processing;
[0045] Step 3: Use the raw materials prepared on the feeding machine to transport them to the automatic distributing machine. After the distributing machine calculates and measures through the formula parameters, it is put into the buffer bin, and is quantitatively transported to the m...
PUM
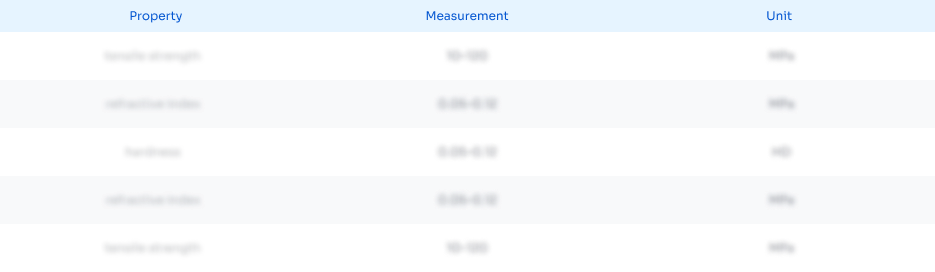
Abstract
Description
Claims
Application Information

- R&D
- Intellectual Property
- Life Sciences
- Materials
- Tech Scout
- Unparalleled Data Quality
- Higher Quality Content
- 60% Fewer Hallucinations
Browse by: Latest US Patents, China's latest patents, Technical Efficacy Thesaurus, Application Domain, Technology Topic, Popular Technical Reports.
© 2025 PatSnap. All rights reserved.Legal|Privacy policy|Modern Slavery Act Transparency Statement|Sitemap|About US| Contact US: help@patsnap.com