Preparation method of CoFe2O4/F-Ag2MoO4 composite material
A composite material, deionized water technology, applied in electrodes, electrolysis process, electrolysis components, etc., can solve the problems of poor catalyst stability, difficult catalyst catalysis reaction, etc., to achieve easy access, excellent electrocatalytic performance, and improved electrocatalytic performance. Effect
- Summary
- Abstract
- Description
- Claims
- Application Information
AI Technical Summary
Problems solved by technology
Method used
Image
Examples
Embodiment 1
[0022] a CoFe 2 o 4 / F-Ag 2 MoO 4 The composite material specifically comprises the following preparation steps:
[0023] (1) Dissolve 4g of cobalt nitrate and 2g of ferric nitrate in deionized water. After the dissolution is complete, transfer it to a polytetrafluoroethylene reactor, and conduct a hydrothermal reaction at 180°C for 24 hours. After the product is cooled, wash it with deionized water 3 times, dry at 60°C;
[0024] (2) Add 2mmol Na 2 MoO 4 2H 2 O dissolved in 100ml deionized water, 8mmolAgNO 3 Dissolve in 50ml of deionized water, then mix the two solutions, stir at 800r / min for 1h, then sonicate for 30min, then add 4mmol NaF and 4g of the product of step (1), and continue stirring for 1h;
[0025] (3) Transfer the solution of step (2) into a polytetrafluoroethylene reactor, conduct a hydrothermal reaction at 160°C for 24 hours, then centrifuge and wash at 8000rpm / min, and dry in vacuum to obtain CoFe 2 o 4 / F-Ag 2 MoO 4 composite material.
[0026] ...
Embodiment 2
[0037] a CoFe 2 o 4 / F-Ag 2 MoO 4 The composite material specifically comprises the following preparation steps:
[0038] (1) Dissolve 4g of cobalt nitrate and 1g of ferric nitrate in deionized water. After the dissolution is complete, transfer it to a polytetrafluoroethylene reactor, and conduct a hydrothermal reaction at 150°C for 16 hours. After the product is cooled, wash it with deionized water 3 times, dry at 60°C;
[0039] (2) Add 2mmol Na 2 MoO 4 2H 2 O dissolved in 100ml deionized water, 4mmolAgNO 3 Dissolve in 50ml of deionized water, then mix the two solutions, stir at 800r / min for 1h, then sonicate for 30min, then add 2mmol NaF and 2g of the product of step (1), and continue stirring for 1h;
[0040] (3) Transfer the solution of step (2) into a polytetrafluoroethylene reactor, conduct a hydrothermal reaction at 140°C for 16 hours, then centrifuge and wash at 6000rpm / min, and dry in vacuum to obtain CoFe 2 o 4 / F-Ag 2 MoO 4 composite material.
[0041] ...
Embodiment 3
[0043] a CoFe 2 o 4 / F-Ag 2 MoO 4 The composite material specifically comprises the following preparation steps:
[0044] (1) Dissolve 4g of cobalt nitrate and 3g of ferric nitrate in deionized water. After the dissolution is complete, transfer it to a polytetrafluoroethylene reactor, and conduct a hydrothermal reaction at 200°C for 32 hours. After the product is cooled, wash it with deionized water 3 times, dry at 60°C;
[0045] (2) Add 2mmol Na 2 MoO 4 2H 2 O dissolved in 100ml deionized water, 12mmol AgNO 3 Dissolve in 50ml of deionized water, then mix the two solutions, stir at 800r / min for 1h, then sonicate for 30min, then add 6mmolNaF and 6g of the product of step (1), and continue stirring for 1h;
[0046] (3) Transfer the solution of step (2) into a polytetrafluoroethylene reactor, conduct a hydrothermal reaction at 180°C for 32 hours, then centrifuge and wash at 10,000rpm / min, and dry in vacuum to obtain CoFe 2 o 4 / F-Ag 2 MoO 4 composite material.
[004...
PUM
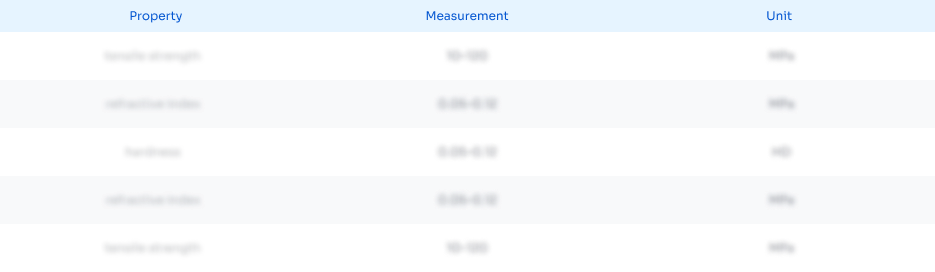
Abstract
Description
Claims
Application Information

- R&D
- Intellectual Property
- Life Sciences
- Materials
- Tech Scout
- Unparalleled Data Quality
- Higher Quality Content
- 60% Fewer Hallucinations
Browse by: Latest US Patents, China's latest patents, Technical Efficacy Thesaurus, Application Domain, Technology Topic, Popular Technical Reports.
© 2025 PatSnap. All rights reserved.Legal|Privacy policy|Modern Slavery Act Transparency Statement|Sitemap|About US| Contact US: help@patsnap.com