Process for preparing consumable electrode for electric arc melting by utilizing CuCr alloy powder material
A consumable electrode and arc smelting technology, applied in the field of consumable electrode preparation, can solve the problems of uneven mixing of mixed powder, affecting the performance of contact materials, and increasing the temperature of the molten pool, achieving good uniformity and optimizing microscopic The effect of organizing and reducing the temperature of the molten pool
- Summary
- Abstract
- Description
- Claims
- Application Information
AI Technical Summary
Problems solved by technology
Method used
Image
Examples
Embodiment 1
[0030] Embodiment 1: A process for preparing consumable electrodes for arc smelting using CuCr alloy powder materials, specifically comprising:
[0031] Step 1: Preparation of CuCr alloy powder material
[0032] Prepare a CuCr alloy powder material with a chromium content of 1%wt; wherein, the CuCr alloy powder material is specifically CuCr alloy powder;
[0033] The specific preparation method of CuCr alloy powder is:
[0034] 1) Ingredients: by weight percentage, the percentage content of each element in the raw material is: Cr 1%, Cu balance, take the required copper powder and chromium powder for later use; wherein, the Cr element adopts 99.99% high-purity metal Chromium powder, Cu element adopts 99.99% high-purity metal copper powder;
[0035] 2) mixing: the spare copper powder and chromium powder were ball milled for 3 hours under vacuum to obtain mixed powder;
[0036] 3) Melting: melt the mixed powder obtained in step 2) in a vacuum induction melting furnace; specif...
Embodiment 2
[0044] Embodiment 2: A process for preparing consumable electrodes for arc smelting using CuCr alloy powder materials, specifically comprising:
[0045] Step 1: Preparation of CuCr alloy powder material
[0046] Prepare a CuCr alloy powder material with a chromium content of 40%wt; wherein, the CuCr alloy powder material is specifically CuCr alloy powder;
[0047] The specific preparation method of CuCr alloy powder is:
[0048] 1) Ingredients: by weight percentage, the percentage content of each element in the raw material is: Cr 40%, Cu balance, take the required copper powder and chromium powder for later use; wherein, the Cr element adopts 99.99% high-purity metal Chromium powder, Cu element adopts 99.99% high-purity metal copper powder;
[0049] 2) mixing: the spare copper powder and chromium powder were ball milled for 4 hours under vacuum to obtain mixed powder;
[0050] 3) Melting: melt the mixed powder obtained in step 2) in a vacuum induction melting furnace; spec...
Embodiment 3
[0058] Embodiment 3: A process for preparing consumable electrodes for arc smelting using CuCr alloy powder materials, specifically comprising:
[0059] Step 1: Preparation of CuCr alloy powder material
[0060] Prepare a CuCr alloy powder material with a chromium content of 50%wt; wherein, the CuCr alloy powder material is specifically CuCr alloy powder;
[0061] The specific preparation method of CuCr alloy powder is:
[0062] 1) Ingredients: by weight percentage, the percentage content of each element in the raw material is: Cr 50%, Cu balance, take the required copper powder and chromium powder for later use; wherein, the Cr element adopts 99.99% high-purity metal Chromium powder, Cu element adopts 99.99% high-purity metal copper powder;
[0063] 2) mixing: the spare copper powder and chromium powder were ball milled for 5 hours under vacuum to obtain mixed powder;
[0064] 3) Melting: melt the mixed powder obtained in step 2) in a vacuum induction melting furnace; spec...
PUM
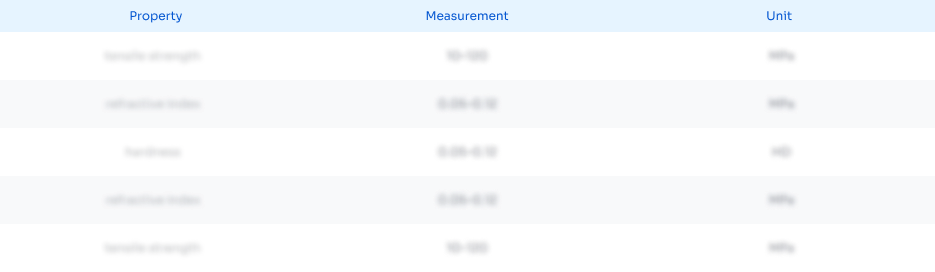
Abstract
Description
Claims
Application Information

- R&D
- Intellectual Property
- Life Sciences
- Materials
- Tech Scout
- Unparalleled Data Quality
- Higher Quality Content
- 60% Fewer Hallucinations
Browse by: Latest US Patents, China's latest patents, Technical Efficacy Thesaurus, Application Domain, Technology Topic, Popular Technical Reports.
© 2025 PatSnap. All rights reserved.Legal|Privacy policy|Modern Slavery Act Transparency Statement|Sitemap|About US| Contact US: help@patsnap.com