An aluminum alloy welded sub-frame formed by hydraulic tube expansion
A technology of aluminum alloy and sub-frame, which is applied to vehicle parts, substructure, transportation and packaging, etc. It can solve the problems of high difficulty in installation and disassembly, increase of body weight, low precision, etc., achieve good vibration isolation effect and reduce operation Difficulty, the effect of improving the rigidity of the connection
- Summary
- Abstract
- Description
- Claims
- Application Information
AI Technical Summary
Problems solved by technology
Method used
Image
Examples
Embodiment Construction
[0023] Next, the technical solutions in the embodiments of the present invention will be described in connection with the drawings of the embodiments of the present invention, and it is understood that the described embodiments are merely the embodiments of the present invention, not all of the embodiments. Based on the embodiments of the present invention, all other embodiments obtained by those of ordinary skill in the art are in the range of the present invention without making creative labor premise.
[0024] See Figure 1-6 A hydro-welded aluminum tube forming the sub-frame, the seat 1 includes a shock stable, stable damper seat 2 and the plate 1 from stable composition cushion 3, a cushion 3 is fixedly mounted on the front stabilizer plate 2 , fixed to the back plate 2 is connected to a stable X-type stabilizing guide member 4, X-type stabilizer guide member 2 and the central position of the stabilization plate 4 defines a mounting groove 5, X-shaped guide member form a stabl...
PUM
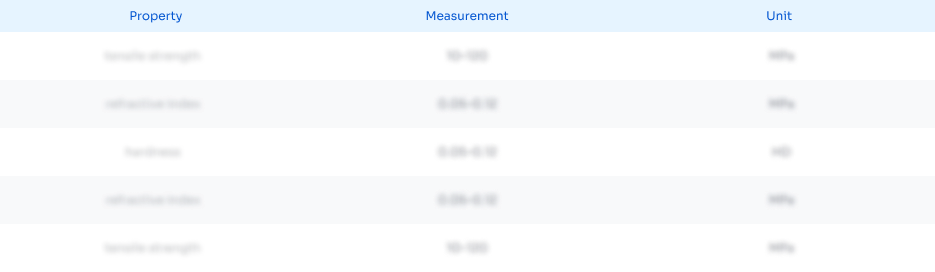
Abstract
Description
Claims
Application Information

- R&D
- Intellectual Property
- Life Sciences
- Materials
- Tech Scout
- Unparalleled Data Quality
- Higher Quality Content
- 60% Fewer Hallucinations
Browse by: Latest US Patents, China's latest patents, Technical Efficacy Thesaurus, Application Domain, Technology Topic, Popular Technical Reports.
© 2025 PatSnap. All rights reserved.Legal|Privacy policy|Modern Slavery Act Transparency Statement|Sitemap|About US| Contact US: help@patsnap.com