Plastic master-batch continuous processing method
A processing method and technology of plastic masterbatch, applied in coating and other directions, can solve the problems of slow drying process, occupying site space, affecting the continuous dehumidification and drying effect of plastic particles, etc., to improve uniformity and drying efficiency. Effect
- Summary
- Abstract
- Description
- Claims
- Application Information
AI Technical Summary
Problems solved by technology
Method used
Image
Examples
Embodiment 1
[0047] see Figure 1-3 , a method for continuously processing plastic masterbatches, comprising the following steps:
[0048] S1. Weigh a certain mass ratio of epoxy resin, bentonite, dispersant, compatibilizer, antibacterial agent, binder, film-forming agent, and plasticizer to obtain a mixture by melting and blending, and import the mixture into a twin-screw extruder extrusion molding;
[0049] S2. The masterbatch formed in S1 is automatically screened by the vibrating screen according to the size of the masterbatch, and the mixing and heat removal device is installed in the dehumidification cylinder 1 with the head 2 installed. The mixing and heat removal device is installed at the bottom of the head 2. At the end, the first motor that drives the mixing and heat removal device is installed on the head 2;
[0050] S3. Introduce the masterbatch into the dehumidification cylinder 1, rotate the moisture-absorbing column on the mixing and heat-dispelling device, and use the fi...
PUM
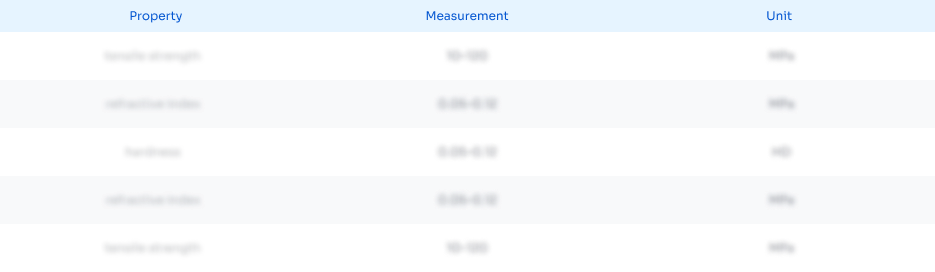
Abstract
Description
Claims
Application Information

- Generate Ideas
- Intellectual Property
- Life Sciences
- Materials
- Tech Scout
- Unparalleled Data Quality
- Higher Quality Content
- 60% Fewer Hallucinations
Browse by: Latest US Patents, China's latest patents, Technical Efficacy Thesaurus, Application Domain, Technology Topic, Popular Technical Reports.
© 2025 PatSnap. All rights reserved.Legal|Privacy policy|Modern Slavery Act Transparency Statement|Sitemap|About US| Contact US: help@patsnap.com