Hypereutectic aluminum-silicon alloy ultra-long-term dual modification method
An aluminum-silicon alloy and hypereutectic technology, which is applied in the field of long-term double metamorphism of hypereutectic aluminum-silicon alloy, can solve the problems of waste, difficulty, and short effective time of metamorphism.
- Summary
- Abstract
- Description
- Claims
- Application Information
AI Technical Summary
Problems solved by technology
Method used
Image
Examples
Embodiment 1
[0040] 1) Ingredients:
[0041] A hypereutectic aluminum-silicon alloy ingredients: Weigh 87 kg of A00 aluminum ingot and 13 kg of industrial silicon;
[0042] B prepares the fluoride salt according to the weight of the aluminum-silicon alloy, formula principle: ①Si / Ti+Zr+B+C=2, ②Ti, Zr, B, C molar ratio is Ti:Zr:B:C=1:1:2: 2. Potassium fluotitanate needs to be weighed to be 8.6 kg (according to 98% absorption rate); wherein potassium fluozirconate needs to be weighed to be 10.1 kg (according to 99% absorption rate); potassium fluoborate to be weighed is 8.9 kg (according to 98% absorption rate), weighing graphene is 1.1 kilograms (by 80% absorption rate);
[0043] 2) In situ reaction:
[0044] Put the original aluminum ingots and industrial silicon into the intermediate frequency furnace, start the furnace to heat up, after the aluminum ingots and industrial silicon are completely melted, remove the surface scum, measure the temperature of the aluminum water at 700°C, first...
Embodiment 2
[0050] 1) Ingredients:
[0051] A Hypereutectic aluminum-silicon alloy ingredients: Weigh 80 kg of A00 aluminum ingot and 20 kg of industrial silicon;
[0052] B prepares fluorine salt according to the weight of aluminum-silicon alloy, formula principle: ①Si / Ti+Zr+B+C=3.5, ②Ti, Zr, B, C molar ratio is Ti:B:C=1:1:2:2, Potassium fluotitanate which needs to be weighed is 7.6 kilograms (according to 98% absorption rate); wherein needs to weigh potassium fluozirconate to be 8.9 kilograms (according to 99% absorption rate); absorption rate), weighing graphene is 0.93 kilograms (by 80% absorption rate); 2) in situ reaction:
[0053] Put the original aluminum ingot and industrial silicon into the intermediate frequency furnace, start the furnace to heat up, after the aluminum ingot and industrial silicon are completely melted, remove the surface scum, control the temperature of the aluminum water to 720°C, first add potassium fluoroborate, and react for 10 minutes; Add the prepared ...
Embodiment 3
[0059] 1) Ingredients:
[0060] A hypereutectic aluminum-silicon alloy ingredients: Weigh 75 kg of A00 aluminum ingot and 25 kg of industrial silicon;
[0061] B prepares fluorine salt according to the weight of aluminum-silicon alloy, formula principle: ①Si / Ti+Zr+B+C=5, ②Ti, Zr, B, C molar ratio is Ti:B:C=1:1:2:2, Potassium fluotitanate which needs to be weighed is 6.6 kilograms (according to 98% absorption rate); wherein needs to weigh potassium fluozirconate to be 7.8 kilograms (according to 99% absorption rate); Absorption rate), weighing graphene is 0.81 kilogram (by 80% absorption rate);
[0062] 2) In situ reaction:
[0063] Put the original aluminum ingot and industrial silicon into the intermediate frequency furnace, start the furnace to heat up, after the aluminum ingot and industrial silicon are completely melted, remove the surface scum, control the temperature of the aluminum water to 750°C, first add potassium fluoroborate, and react for 10 minutes; Add the pr...
PUM
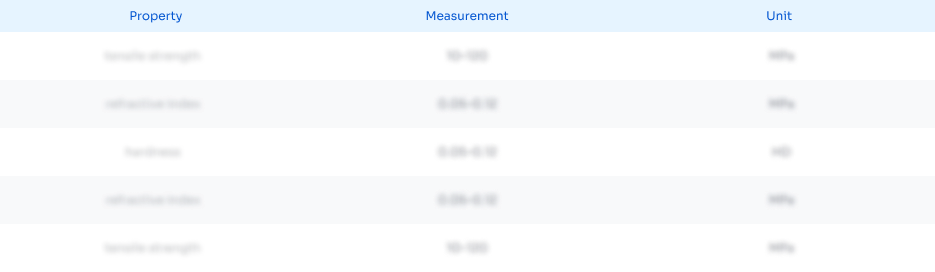
Abstract
Description
Claims
Application Information

- Generate Ideas
- Intellectual Property
- Life Sciences
- Materials
- Tech Scout
- Unparalleled Data Quality
- Higher Quality Content
- 60% Fewer Hallucinations
Browse by: Latest US Patents, China's latest patents, Technical Efficacy Thesaurus, Application Domain, Technology Topic, Popular Technical Reports.
© 2025 PatSnap. All rights reserved.Legal|Privacy policy|Modern Slavery Act Transparency Statement|Sitemap|About US| Contact US: help@patsnap.com