Butterfly valve body casting process
A casting process and valve body technology, which is applied in the field of disc valve body casting process, can solve problems such as shrinkage cavity, inconsistent cooling, and product scrapping, and achieve the effects of solving shrinkage cavity, preventing shrinkage cavity phenomenon, and facilitating installation
- Summary
- Abstract
- Description
- Claims
- Application Information
AI Technical Summary
Problems solved by technology
Method used
Image
Examples
Embodiment Construction
[0034] The following examples can enable those skilled in the art to understand the present invention more comprehensively, but the present invention is not limited to the scope of the described examples.
[0035] Disc valve body casting process of the present invention is realized through the following steps:
[0036] S1 Mold manufacturing: First, design the mold drawing according to the product drawing, and manufacture a special mold according to the mold drawing, and check whether the mold is qualified.
[0037] Special mold includes
[0038] A core box body 1, such as Figure 1-Figure 4 As can be seen from the schematic diagram shown, the core box main body 1 is in the shape of a ring, and the inside of the core box main body 1 is a sand core cavity 2, and the first protruding blocks 3 and the second protruding blocks are sequentially distributed on the peripheral surface of the core box main body 1. Block 4, the third bump 5, the fourth bump 6, and the first bump 3 has ...
PUM
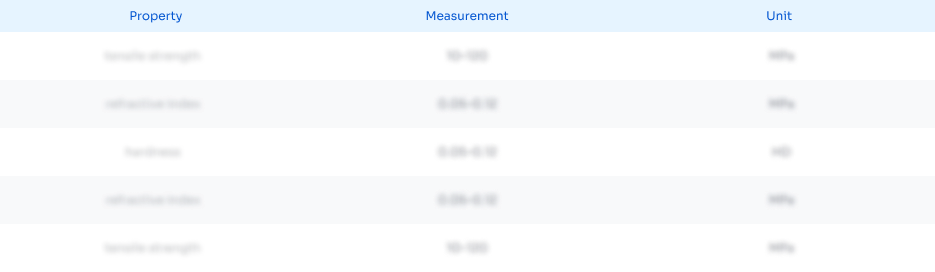
Abstract
Description
Claims
Application Information

- R&D
- Intellectual Property
- Life Sciences
- Materials
- Tech Scout
- Unparalleled Data Quality
- Higher Quality Content
- 60% Fewer Hallucinations
Browse by: Latest US Patents, China's latest patents, Technical Efficacy Thesaurus, Application Domain, Technology Topic, Popular Technical Reports.
© 2025 PatSnap. All rights reserved.Legal|Privacy policy|Modern Slavery Act Transparency Statement|Sitemap|About US| Contact US: help@patsnap.com