Flue gas cooler capable of adjusting flue gas flow speed on line
A flue gas cooler and flue gas flow rate technology, applied in the field of coal-fired power plant boilers, can solve the problems of flue gas cooler leakage, local ash accumulation blockage, fly ash viscosity, etc., to increase the flue gas flow rate and eliminate ash blockage Problems and solutions to the effect of excessively large flue gas flow rates
- Summary
- Abstract
- Description
- Claims
- Application Information
AI Technical Summary
Problems solved by technology
Method used
Image
Examples
Embodiment Construction
[0023] The present invention will be further described in detail below in conjunction with the accompanying drawings and embodiments.
[0024] see Figure 1-4 , the flue gas cooler capable of adjusting the flue gas flow rate on-line in the present invention includes a shell and multiple sets of heat exchange modules 1 arranged inside the shell, and the shell is arranged between the air preheater 6 and the dust collector 7 of the coal-fired power plant boiler in the flue between. The heat exchange modules 1 are separated by flue plates 2. The heat exchange modules 1 are connected by several heat exchange tubes 3, and along the flow direction of the flue gas, an adjustable flue gas is installed behind the last heat exchange tube 3. Gas baffle 4. Each set of heat exchange modules 1 is provided with a pressure measuring point 5 at the front and rear respectively, and the number of pressure measuring points 5 is twice the number of heat exchange modules 1 . The flue gas cooler c...
PUM
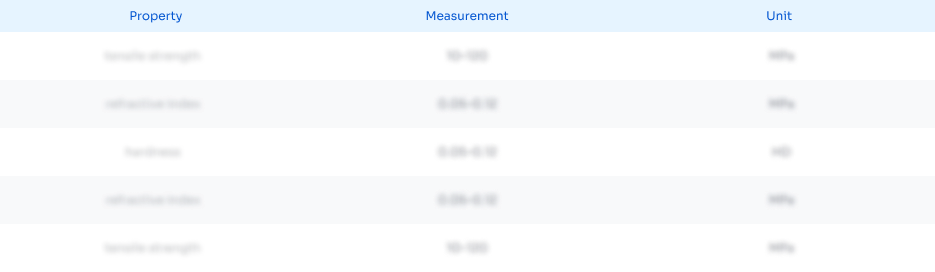
Abstract
Description
Claims
Application Information

- Generate Ideas
- Intellectual Property
- Life Sciences
- Materials
- Tech Scout
- Unparalleled Data Quality
- Higher Quality Content
- 60% Fewer Hallucinations
Browse by: Latest US Patents, China's latest patents, Technical Efficacy Thesaurus, Application Domain, Technology Topic, Popular Technical Reports.
© 2025 PatSnap. All rights reserved.Legal|Privacy policy|Modern Slavery Act Transparency Statement|Sitemap|About US| Contact US: help@patsnap.com