Method for synthesizing alpha-fluorinated thioacrylamide derivative
A technology for substituting acrylamide and trifluoroacrylamide, which is applied in the field of preparation of α-fluorinated thioacrylamide derivatives, can solve the problems of practicality and applicability limitations, harsh reaction conditions, and difficult preparation of raw materials, etc. Healthy operators, easy operation and excellent productivity
- Summary
- Abstract
- Description
- Claims
- Application Information
AI Technical Summary
Problems solved by technology
Method used
Image
Examples
specific Embodiment 1
[0025] Specific embodiment one: with 20.3 milligrams (0.1mmol) 3,3,3-trifluoro-N-phenylpropanamide, 12.3 milligrams (0.05mmol) 4,4'-dimethyl diphenyl disulfide, 1.9 milligrams ( 0.01mmol) cuprous iodide, 55.3mg (0.4mmol) potassium carbonate, 15.7mg (0.06mmol) triphenylphosphine, 9.0mg (0.5mmol) water were added to 2ml solvent tetrahydrofuran. The reaction was stirred at 80°C for 12 hours. Cool after the reaction, filter the reaction solution to obtain the filtrate, and use a rotary evaporator to remove the solvent to obtain the residue, and the residue is rinsed with an eluent prepared with petroleum ether and ethyl acetate at a volume ratio of 10:1 through a silica gel column. Wash, collect the effluent according to the actual gradient, detect by TLC, combine the effluent containing the target product, use a rotary evaporator to remove the solvent from the combined effluent, and dry in vacuo to obtain a yellow solid 3-fluoro-N-phenyl-3 -(p-tolyl)acrylamide 23.8 mg, yield 83%...
specific Embodiment 2
[0026]Specific example two: 20.3 mg (0.1 mmol) 3,3,3-trifluoro-N-phenylpropanamide, 10.9 mg (0.05 mmol) diphenyl disulfide, 1.9 mg (0.01 mmol) cuprous iodide, 55.3 mg (0.4 mmol) of potassium carbonate, 15.7 mg (0.06 mmol) of triphenylphosphine, and 9.0 mg (0.5 mmol) of water were added to 2 ml of solvent tetrahydrofuran. The reaction was stirred at 80°C for 12 hours. Cool after the reaction, filter the reaction solution to obtain the filtrate, and use a rotary evaporator to remove the solvent to obtain the residue. The residue is rinsed with an eluent prepared with petroleum ether and ethyl acetate at a volume ratio of 10:1 through a silica gel column. Wash, collect the effluent according to the actual gradient, detect by TLC, combine the effluent containing the target product, use a rotary evaporator to remove the solvent from the combined effluent, and dry in vacuo to obtain a yellow solid 3-fluoro-N-phenyl-3 -(phenylthio)acrylamide 20.7 mg, yield 76%. 1H NMR (400MHz, CDCl...
specific Embodiment 3
[0027] Specific example three: 20.3 mg (0.1 mmol) 3,3,3-trifluoro-N-phenylpropanamide, 13.9 mg (0.05 mmol) 4,4'-dimethoxydiphenyl disulfide, 1.9 mg (0.01 mmol) cuprous iodide, 55.3 mg (0.4 mmol) potassium carbonate, 15.7 mg (0.06 mmol) triphenylphosphine, 9.0 mg (0.5 mmol) water were added to 2 ml solvent tetrahydrofuran. The reaction was stirred at 80°C for 12 hours. Cool after the reaction, filter the reaction solution to obtain the filtrate, and use a rotary evaporator to remove the solvent to obtain the residue. The residue is rinsed with an eluent prepared with petroleum ether and ethyl acetate at a volume ratio of 10:1 through a silica gel column. Wash, collect the effluent according to the actual gradient, detect by TLC, combine the effluent containing the target product, remove the solvent by rotating the combined effluent with a rotary evaporator, and dry in vacuo to obtain a yellow solid 3-fluoro-3-((4- Methoxyphenyl)thio)-N-phenylacrylamide 19.7 mg, yield 65%. 1H ...
PUM
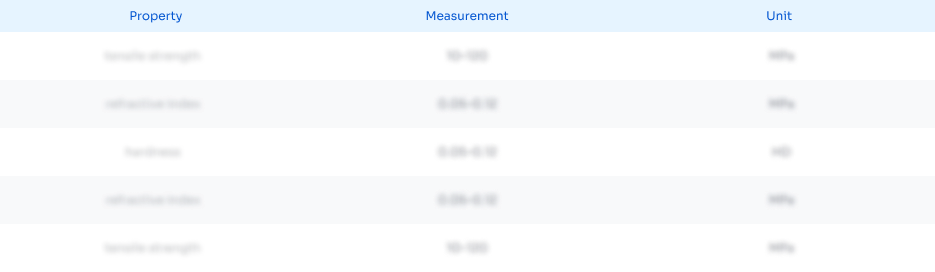
Abstract
Description
Claims
Application Information

- R&D Engineer
- R&D Manager
- IP Professional
- Industry Leading Data Capabilities
- Powerful AI technology
- Patent DNA Extraction
Browse by: Latest US Patents, China's latest patents, Technical Efficacy Thesaurus, Application Domain, Technology Topic, Popular Technical Reports.
© 2024 PatSnap. All rights reserved.Legal|Privacy policy|Modern Slavery Act Transparency Statement|Sitemap|About US| Contact US: help@patsnap.com