Low-carbon aluminum-containing steel and smelting control method thereof
A control method, aluminum steel technology, applied in the field of iron and steel smelting, can solve the problems of affecting steel quality, nozzle nodules, unable to realize multi-furnace continuous pouring, etc.
- Summary
- Abstract
- Description
- Claims
- Application Information
AI Technical Summary
Problems solved by technology
Method used
Image
Examples
Embodiment 1
[0113] For the production of a certain steel type, the composition control requirements of the finished product are: C: 0.04-0.07%, Si: ≤0.08%, Mn: 0.15-0.25%, Als: 0.010-0.025%, P: ≤0.025%, S: 0.025%.
[0114] The specific steps are: the carbon at the end of the converter is controlled at 0.08%, the tapping temperature is ≥ 1640°C, VD treatment is performed, the high vacuum time is 8 minutes, the oxygen is fixed at the end of VD, and Al is adjusted to 0.025%. Then LF treatment, LF added lime 5.5kg / t, synthetic slag 8.5kg / t. And control the composition of refining slag to include: CaO 60-65%, SiO 2 ≤6%, Al 2 o 3 30~35%, MgO 3~8%, TFe+MnO≤1.0%; refining slag alkalinity≥10. After the slag is melted, 0.5kg / t of aluminum particles are added through the silo, and 0.8kg / t of aluminum particles are added by hand. During this process, argon gas is blown from the bottom, and the flow rate of argon gas is controlled at 30Nm 3 / h. Raise the temperature to 1580°C for strong stirring...
Embodiment 2
[0116] For the production of a certain steel type, the composition control requirements of the finished product are: C: 0.05-0.07%, Si: ≤0.08%, Mn: 0.35-0.50%, Al: 0.025-0.040%, P: ≤0.025%, S: 0.025%.
[0117] The specific steps are: the carbon at the end of the converter is controlled at 0.12%, the tapping temperature is ≥1640°C, VD treatment is performed, the high vacuum time is 12 minutes, the oxygen is fixed at the end of VD, Al is adjusted to 0.025%, and then LF treatment is performed, and 4.5kg of lime is added to LF / t, synthetic slag 6.5kg / t, and control the composition of refining slag including: CaO 60-65%, SiO 2 ≤6%, Al 2 o 3 30~35%, MgO 3~8%, TFe+MnO≤1.0%; refining slag alkalinity≥10. After the slag is melted, 0.4kg / t of aluminum pellets are added through the silo, and 0.6kg / t of aluminum pellets are thrown by hand. During this process, argon gas is blown from the bottom, and the flow rate of argon gas is controlled at 60Nm 3 / h. Before sampling 1, the tempera...
Embodiment 3
[0119] It is basically the same as that of Example 1, except that the VD ends the oxygen determination, and the Al is adjusted to 0.020%.
PUM
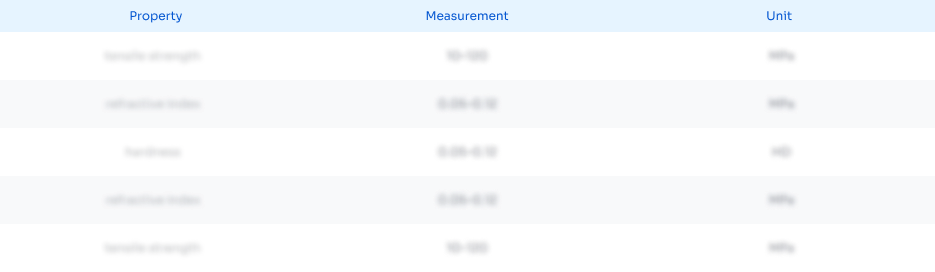
Abstract
Description
Claims
Application Information

- R&D
- Intellectual Property
- Life Sciences
- Materials
- Tech Scout
- Unparalleled Data Quality
- Higher Quality Content
- 60% Fewer Hallucinations
Browse by: Latest US Patents, China's latest patents, Technical Efficacy Thesaurus, Application Domain, Technology Topic, Popular Technical Reports.
© 2025 PatSnap. All rights reserved.Legal|Privacy policy|Modern Slavery Act Transparency Statement|Sitemap|About US| Contact US: help@patsnap.com