Method for reducing magnesium oxide in ferronickel slag and method for preparing mineral wool
A technology of ferronickel slag and magnesium oxide, which is applied in the field of metallurgy, can solve the problems of forming solid particles, high melting point, and poor quality of mineral wool, and achieve the effect of reducing the content of magnesium oxide and improving reaction efficiency
- Summary
- Abstract
- Description
- Claims
- Application Information
AI Technical Summary
Problems solved by technology
Method used
Image
Examples
Embodiment 1
[0046] The method that present embodiment prepares slag wool, comprises following process:
[0047] The slag temperature of the ferronickel smelting furnace is 1400°C. The impregnated carbon is put into the slag bag in advance, the molten nickel-iron slag is put into the slag bag, and then the slag mixed with the impregnated carbon in the slag bag is poured into the heat preservation electric furnace. Insulated at 1500 for 1 hour, at this time, the mass percentage of magnesium oxide in the ferronickel slag was sampled and detected to be 20.5%; then it was further prepared into slag wool, and the cotton-forming rate of the obtained slag wool was increased by 5%.
[0048] Among them, in the impregnated carbon used in this embodiment, the carbonaceous material is semi-coke, the fixed carbon content in the semi-coke is 73.5%, the molar ratio of the carbon in the impregnated carbon to the magnesium oxide in the ferronickel slag is 1:2, the impregnated The molar ratio of calcium chl...
Embodiment 2
[0050] The method that present embodiment prepares slag wool, comprises following process:
[0051] The slag temperature of the ferronickel smelting furnace is 1500°C. The impregnated carbon is put into the slag bag in advance, the molten nickel-iron slag is put into the slag bag, and then the slag mixed with the impregnated carbon in the slag bag is poured into the heat preservation electric furnace. It was kept at 1550° C. for 3 hours. At this time, the mass percent content in the ferronickel slag was 17.3% by sampling and detection; then it was further prepared into slag wool, and the cotton-forming rate of the obtained slag wool was increased by 10%.
[0052] Wherein, in the impregnated carbon used in this embodiment, the carbonaceous material is semi-coke, the fixed carbon content in the semi-coke is 73.5%, the molar ratio of the carbon in the impregnated carbon to the magnesium oxide in the ferronickel slag is 1:1, and the impregnated The molar ratio of calcium chloride ...
Embodiment 3
[0054] The method that present embodiment prepares slag wool, comprises following process:
[0055] The slag temperature of ferronickel smelting slag is 1500℃, the impregnated carbon is put into the slag bag in advance, the molten nickel-iron slag is put into the slag bag, and then the slag mixed with impregnated carbon in the slag bag is poured into the heat preservation electric furnace, at 1600 At this time, the mass percentage of magnesium oxide in the ferronickel slag was 12.1% by sampling and detection; and then further prepared into slag wool, and the cotton-forming rate of the obtained slag wool was increased by 28%.
[0056] Among them, in the impregnated carbon used in this embodiment, the carbonaceous material is semi-coke, the fixed carbon content in the semi-coke is 73.5%, and the molar ratio of the carbon in the impregnated carbon to the magnesium oxide in the ferronickel slag is 1:0.5. The molar ratio of calcium chloride in carbon to magnesium oxide in ferronick...
PUM
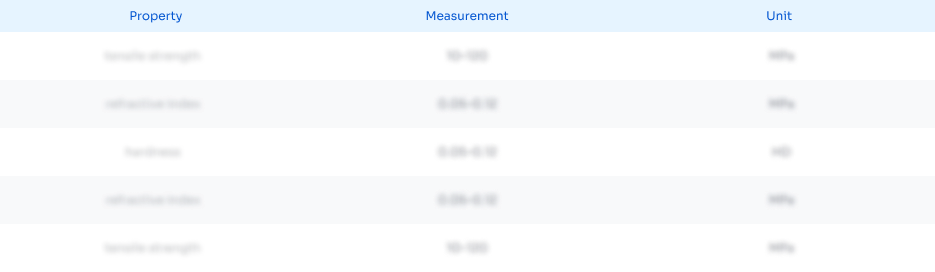
Abstract
Description
Claims
Application Information

- R&D Engineer
- R&D Manager
- IP Professional
- Industry Leading Data Capabilities
- Powerful AI technology
- Patent DNA Extraction
Browse by: Latest US Patents, China's latest patents, Technical Efficacy Thesaurus, Application Domain, Technology Topic, Popular Technical Reports.
© 2024 PatSnap. All rights reserved.Legal|Privacy policy|Modern Slavery Act Transparency Statement|Sitemap|About US| Contact US: help@patsnap.com