Direct torque control method for five-phase permanent magnet synchronous motor with one-phase fault
A technology of direct torque control and permanent magnet synchronous motors, which is applied in motor control, motor generator control, AC motor control, etc., can solve problems such as complex control process, achieve simplification of control process, easy implementation, and normal operation Effect
- Summary
- Abstract
- Description
- Claims
- Application Information
AI Technical Summary
Problems solved by technology
Method used
Image
Examples
Embodiment Construction
[0076] The present invention will be described in detail below in conjunction with the accompanying drawings and specific embodiments.
[0077] The direct torque control method of the five-phase permanent magnet synchronous motor in the present invention is implemented according to the following steps:
[0078] Step 1. According to the switching state of each bridge arm of the five-phase inverter and the DC bus voltage U dc Get the phase voltage of each stator of the five-phase PMSM, and then transform the A-B-C-D-E natural coordinate system to α through the static coordinate transformation matrix of the five-phase PMSM during normal operation 1 -β 1 -α 3 -β 3 -0 coordinate system, get α 1 -β 1 and alpha 3 -β 3 The voltage vector distribution diagram of the subspace is shown in Fig. 2(a) and Fig. 2(b);
[0079] Step 1 is as follows:
[0080] Step 1.1, the topology of the five-phase PMSM main circuit is as follows figure 1 As shown, for a five-phase inverter, the swit...
PUM
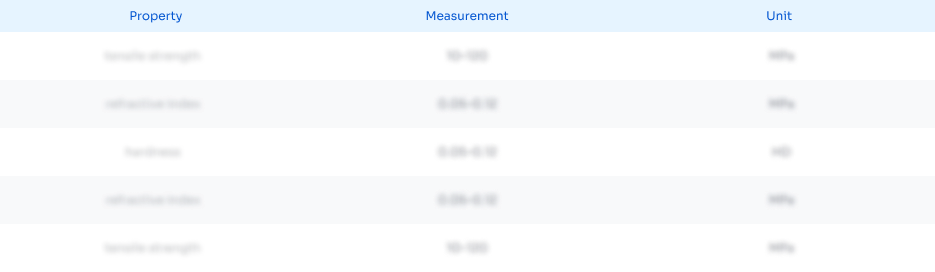
Abstract
Description
Claims
Application Information

- Generate Ideas
- Intellectual Property
- Life Sciences
- Materials
- Tech Scout
- Unparalleled Data Quality
- Higher Quality Content
- 60% Fewer Hallucinations
Browse by: Latest US Patents, China's latest patents, Technical Efficacy Thesaurus, Application Domain, Technology Topic, Popular Technical Reports.
© 2025 PatSnap. All rights reserved.Legal|Privacy policy|Modern Slavery Act Transparency Statement|Sitemap|About US| Contact US: help@patsnap.com