Method for establishing and analyzing three-dimensional fracture model of polyethylene under complex stress
A complex stress and model building technology, applied in special data processing applications, instruments, design optimization/simulation, etc., can solve problems such as unsuitable polyethylene materials, reduce experimental material consumption, simple test operations, and low experimental environment requirements Effect
Pending Publication Date: 2021-01-08
CHINA UNIV OF PETROLEUM (EAST CHINA)
View PDF2 Cites 3 Cited by
- Summary
- Abstract
- Description
- Claims
- Application Information
AI Technical Summary
Problems solved by technology
[0005] The analysis methods for failure under complex stress described in the prior art are all designed for metal materials, which are not suitable for polyethylene materials
Method used
the structure of the environmentally friendly knitted fabric provided by the present invention; figure 2 Flow chart of the yarn wrapping machine for environmentally friendly knitted fabrics and storage devices; image 3 Is the parameter map of the yarn covering machine
View moreImage
Smart Image Click on the blue labels to locate them in the text.
Smart ImageViewing Examples
Examples
Experimental program
Comparison scheme
Effect test
Embodiment 1
[0041] This embodiment provides a failure analysis method for polyethylene material under complex stress state, which specifically involves two research methods: experimental test and finite element simulation. The polyethylene material failure analysis method under the complex stress state includes three parts: tension, shear and compression.
the structure of the environmentally friendly knitted fabric provided by the present invention; figure 2 Flow chart of the yarn wrapping machine for environmentally friendly knitted fabrics and storage devices; image 3 Is the parameter map of the yarn covering machine
Login to View More PUM
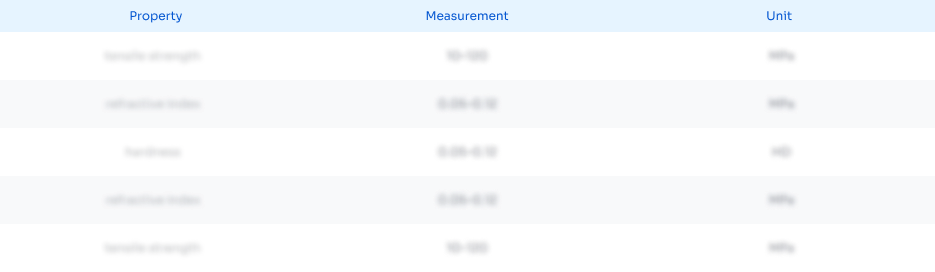
Abstract
The invention relates to the field of laboratory material failure analysis and finite element simulation, in particular to a method for establishing and analyzing a three-dimensional fracture model ofpolyethylene under complex stress. The method comprises the following steps: carrying out a uniaxial tensile experiment on the same polyethylene material to obtain an engineering stress displacementexperiment curve; establishing a finite element model, selecting a damage model, and modifying damage model parameters until an engineering stress displacement curve obtained by a uniaxial tensile experiment can be simulated and reproduced, so as to obtain a real stress-strain curve of a tensile sample; and applying the real stress-strain curve to subsequent finite element simulation, and establishing a three-dimensional fracture model of the polyethylene material in a complex stress state by utilizing finite element analysis. The problem that failure analysis methods under complex stress in the prior art are all designed by metal materials and are not suitable for polyethylene materials is solved.
Description
technical field [0001] The invention relates to the field of laboratory material failure analysis and finite element simulation, in particular to a method for establishing and analyzing a three-dimensional fracture model of polyethylene under complex stress. Background technique [0002] The statements herein merely provide background information related to the present disclosure and may not necessarily constitute prior art. [0003] Polyethylene is a high molecular polymer material, which has the advantages of wear resistance, corrosion resistance, impact resistance, chemical resistance, etc., and is widely used in the pipeline manufacturing industry such as gas pipes and water pipes. In the gas pipe manufacturing industry, polyethylene pipes have become the main pipe type in recent years, especially in the medium and low pressure gas pipeline network. Polyethylene pipes are the main or even the only choice for newly laid pipes and old pipes for repair and renewal. During ...
Claims
the structure of the environmentally friendly knitted fabric provided by the present invention; figure 2 Flow chart of the yarn wrapping machine for environmentally friendly knitted fabrics and storage devices; image 3 Is the parameter map of the yarn covering machine
Login to View More Application Information
Patent Timeline

Patent Type & Authority Applications(China)
IPC IPC(8): G06F30/23G06F119/14
CPCG06F30/23G06F2119/14
Inventor 张毅韩丽美薛世峰曹宇光周博刘翠伟
Owner CHINA UNIV OF PETROLEUM (EAST CHINA)
Features
- R&D
- Intellectual Property
- Life Sciences
- Materials
- Tech Scout
Why Patsnap Eureka
- Unparalleled Data Quality
- Higher Quality Content
- 60% Fewer Hallucinations
Social media
Patsnap Eureka Blog
Learn More Browse by: Latest US Patents, China's latest patents, Technical Efficacy Thesaurus, Application Domain, Technology Topic, Popular Technical Reports.
© 2025 PatSnap. All rights reserved.Legal|Privacy policy|Modern Slavery Act Transparency Statement|Sitemap|About US| Contact US: help@patsnap.com