Comprehensive cutting system for defect removal of wood-plastic plate
A cutting system, defect technology, applied in wood processing appliances, bark area/debris/dust/waste removal, forming/shaping machines, etc., can solve the problem of low processing efficiency, uneven quality of raw boards, affecting thin raw materials problems such as wood board quality, to achieve the effect of improving quality, efficient and stable processing, and improving defect removal efficiency
- Summary
- Abstract
- Description
- Claims
- Application Information
AI Technical Summary
Problems solved by technology
Method used
Image
Examples
Embodiment Construction
[0032] The following will clearly and completely describe the technical solutions in the embodiments of the present invention with reference to the accompanying drawings in the embodiments of the present invention. Obviously, the described embodiments are only some, not all, embodiments of the present invention.
[0033] refer to Figure 1-2 The comprehensive cutting system for wood glue board defect removal includes a frame 1. The frame 1 is provided with a plurality of parallel conveyor belts 2, a cutting blade 4 located between the conveyor belts 2, a detection board 7 for detecting wooden board defects located above the conveyor belt 2, and a feeding roller. 8 and limit roller group 11. The conveyor belt 2 has original power. After the raw wood boards enter the conveyor belt 2, they pass through the cutting blade 4 and the inspection board 7 in sequence. The cutting blade 4 is used to cut the raw boards into strips of equal width, and the inspection board 7 is used to dete...
PUM
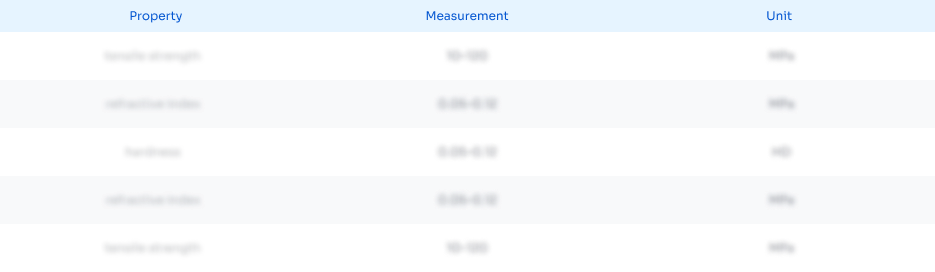
Abstract
Description
Claims
Application Information

- Generate Ideas
- Intellectual Property
- Life Sciences
- Materials
- Tech Scout
- Unparalleled Data Quality
- Higher Quality Content
- 60% Fewer Hallucinations
Browse by: Latest US Patents, China's latest patents, Technical Efficacy Thesaurus, Application Domain, Technology Topic, Popular Technical Reports.
© 2025 PatSnap. All rights reserved.Legal|Privacy policy|Modern Slavery Act Transparency Statement|Sitemap|About US| Contact US: help@patsnap.com