Method for removing residual oxygen in product flow of ethylene preparation by ethane catalytic oxidative dehydrogenation
A technology of catalytic oxidation and oxidative dehydrogenation, applied in chemical instruments and methods, hydrocarbons, hydrocarbons, etc., can solve the problem of high-grade deaerator equipment material, large deaerator processing load, and low deoxygenation reaction efficiency and other problems, to achieve the effect of reducing equipment material requirements, reducing equipment investment and improving recycling rate
- Summary
- Abstract
- Description
- Claims
- Application Information
AI Technical Summary
Problems solved by technology
Method used
Image
Examples
Embodiment 1
[0051] In this example, the diluent gas 2 is nitrogen, the oxygen-containing gas 3 is compressed air, and the production scale is 1 million tons of ethylene per year. A method for removing residual oxygen in the product stream of ethylene by catalytic oxidative dehydrogenation of ethane is given. , the process such as figure 2 As shown, it specifically includes the following steps:
[0052] The ethane raw material 1 from the ethane pretreatment unit, with a flow rate of about 150t / h, is mixed with the diluent gas 2, the oxygen-containing gas 3 and the circulating condensate 17 (ie part of the tank bottom condensate 16) to obtain a mixed feed 5, which is processed The material preheater 16 is preheated to 230°C and then sent to the oxidative dehydrogenation reactor 8 equipped with a catalyst, thereby obtaining at least ethylene, ethane, acetic acid, water, CO and CO 2 The crude product gas 9.
[0053] The obtained crude product gas 9 is connected to the waste heat recovery d...
Embodiment 1 and comparative example 1
[0064] Table 2 embodiment 1 and comparative example 1, deaerator effective reactant concentration and oxygen removal effect
[0065]
[0066]
[0067] From the results in Table 1, it can be found that the feed rate of the deaerator of Example 1 is less than that of the deaerator of Comparative Example 1; this means that the equipment size of the deaerator of Example 1 is smaller than that of Comparative Example 1 The size of the deaerator; the small size means that the equipment investment is low; that is, the investment cost of the deaerator in Example 1 is lower than that of the deaerator in Comparative Example 1. From the results in Table 2, it can be found that in Example 1, the effective reactants in the deaerator feed, such as CO, CH 4 and O 2 The concentration is greater than the effective reactant concentration in Comparative Example 1. This means that the deoxygenation reaction rate of the deaerator of Example 1 is greater than that of Comparative Example 1. ...
Embodiment 2
[0073] In this example, the diluent gas 2 is nitrogen in compressed air, the oxygen-containing gas 3 is compressed air, and the production scale is 800,000 tons of ethylene per year. Oxygen removal method, process flow such as image 3 As shown, it specifically includes the following steps:
[0074] The ethane raw material 1 from the ethane pretreatment unit, with a flow rate of about 122t / h, is mixed with the diluent gas 2, the oxygen-containing gas 3 and the circulating condensate 17 to obtain a mixed feed 5, which is preheated by the feed preheater 2 6' After reaching 210 ° C, the preheated mixed feed 7 is obtained, and sent to the oxidative dehydrogenation reactor 8 equipped with a catalyst, thereby obtaining at least ethylene, ethane, acetic acid, water, CO and CO 2 The crude product gas 9.
[0075] The obtained crude product gas 9 is connected to the waste heat recovery device 10, and the waste heat recovery device 10 recovers the high-temperature waste heat of the cru...
PUM
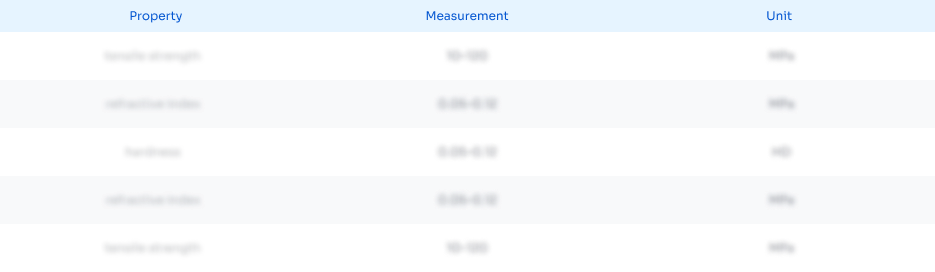
Abstract
Description
Claims
Application Information

- R&D
- Intellectual Property
- Life Sciences
- Materials
- Tech Scout
- Unparalleled Data Quality
- Higher Quality Content
- 60% Fewer Hallucinations
Browse by: Latest US Patents, China's latest patents, Technical Efficacy Thesaurus, Application Domain, Technology Topic, Popular Technical Reports.
© 2025 PatSnap. All rights reserved.Legal|Privacy policy|Modern Slavery Act Transparency Statement|Sitemap|About US| Contact US: help@patsnap.com