Manufacturing method for integrally forming carbon fiber composite material pump body and impeller for pump
A technology of carbon fiber materials and composite materials, applied in applications, home appliances, household components, etc., can solve the problems of complex manufacturing process, low structural strength, pressure deformation, etc., and achieve simple manufacturing process, low cost, and enhanced structural strength Effect
- Summary
- Abstract
- Description
- Claims
- Application Information
AI Technical Summary
Problems solved by technology
Method used
Image
Examples
Embodiment 1
[0043] Carbon fiber epoxy vinyl resin composite material SMC pump body molded in one piece
[0044] Step 1. Configuration and production of the molding material SMC: the selected materials are carbon fiber chopped strands and epoxy vinyl resin.
[0045] 1) Preparation of short carbon fiber filaments: use a wire cutter to chop the loose carbon fiber filaments to a length of 20-25 mm for later use.
[0046] 2) Epoxy vinyl resin configuration: use MFE-752 epoxy vinyl resin, add 1.2%-1.8% MgO, add 0.95%-1.15% curing agent, add 13%-17% low shrinkage agent, add 0.1%-0.2% BYK-W 692, stir at room temperature for 2-4 hours, mix thoroughly.
[0047] 3) Prepare SMC materials: Mix carbon fiber chopped strands and epoxy vinyl resin preparation solution at a ratio of 55:45, use a drum agitator, stir fully for 90-120 minutes, seal and set aside.
[0048] Step 2. Compression molding of the pump body:
[0049] 1) Heating: The temperature of the molding machine is raised to 125°C. The mold ...
Embodiment 2
[0065] Carbon fiber epoxy vinyl resin composite fiber laminated pump body molded in one piece
[0066] Step 1. The configuration and production of the carbon fiber layup of the molded material: the selected materials are carbon fiber chopped strands and epoxy vinyl resin.
[0067] 1) Preparation of carbon fiber fabric: Prepare T300-T600 carbon fiber fabric for use.
[0068] 2) Epoxy vinyl resin configuration: use MFE-752 epoxy vinyl resin, add 1.2%-1.8% MgO, add 0.95%-1.15% curing agent, add 13%-17% low shrinkage agent, add 0.1%-0.2% BYK-W 692, stir at room temperature for 2-4 hours, mix well.
[0069] 3) Making fabric blank material: impregnating the prepared carbon fiber fabric with prepared epoxy vinyl resin on an impregnation machine, controlling the scraper gap, producing a carbon fiber fabric blank roll with a resin content of 48%, and sealing it for later use.
[0070] Step 2. Compression molding of the pump body:
[0071] 1) Heating: The temperature of the molding m...
Embodiment 3
[0087] Carbon fiber epoxy vinyl resin composite material SMC impeller molded in one piece
[0088] Step 1. Configuration and production of the molding material SMC: the selected materials are carbon fiber chopped strands and epoxy vinyl resin.
[0089] 1) Preparation of short carbon fiber filaments: use a wire cutter to chop the loose carbon fiber filaments to a length of 20-25 mm for later use.
[0090] 2) Epoxy vinyl resin configuration: use MFE-752 epoxy vinyl resin, add 1.2%-1.8% MgO, add 0.95%-1.15% curing agent, add 13%-17% low shrinkage agent, add 0.1%-0.2% BYK-W 692, stir at room temperature for 2-4 hours, mix thoroughly.
[0091] 3) Prepare SMC materials: Mix carbon fiber chopped strands and epoxy vinyl resin preparation solution at a ratio of 55:45, use a drum agitator, stir fully for 90-120 minutes, seal and set aside.
[0092] Step 2. Compression molding of the impeller:
[0093] 1) Heating: The temperature of the molding machine is raised to 125°C. The mold is...
PUM
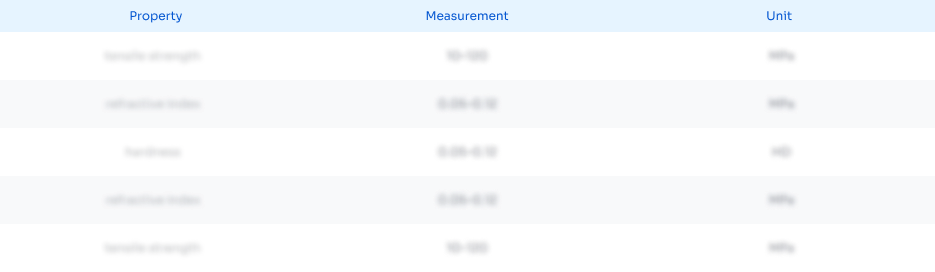
Abstract
Description
Claims
Application Information

- R&D Engineer
- R&D Manager
- IP Professional
- Industry Leading Data Capabilities
- Powerful AI technology
- Patent DNA Extraction
Browse by: Latest US Patents, China's latest patents, Technical Efficacy Thesaurus, Application Domain, Technology Topic, Popular Technical Reports.
© 2024 PatSnap. All rights reserved.Legal|Privacy policy|Modern Slavery Act Transparency Statement|Sitemap|About US| Contact US: help@patsnap.com