Graphene coated tungsten-based hot cathode and preparation method thereof
A graphene and hot cathode technology, which is applied in the manufacture of hot electron cathodes, cold cathodes, and electrode systems, can solve problems such as narrow practicality and scope of application, and gaps in the emission uniformity and stability of cold cathodes.
- Summary
- Abstract
- Description
- Claims
- Application Information
AI Technical Summary
Problems solved by technology
Method used
Image
Examples
Embodiment 1
[0028]Such asfigure 1 As shown, a graphene-coated tungsten-based hot cathode includes a graphene layer 1 and a tungsten base layer 2. The upper surface of the tungsten base layer 2 is covered with a single-layer graphene layer 1. Such asfigure 2As shown in the top view of the structure, the graphene layer-tungsten cathode layer composite structure 3 is placed in the support tube 4 and fixed by the side wall of the support tube 4, and a filament 5 is arranged under the tungsten base layer 2 in the support tube 4 to form a hot cathode. The tungsten base layer 2 and the filament 5 can be directly connected, and a spacer layer 7 can also be added. The anode 6 is arranged relative to the hot cathode, above the hot cathode, and the positional relationship is asfigure 1 Shown. The hot cathode and the anode 6 can adopt a flat structure or a curved structure.
[0029]The preparation method of the above-mentioned graphene-coated tungsten-based hot cathode includes the following steps:
[0030]Step ...
Embodiment 2
[0037]The only difference from Embodiment 1 is that the graphene-coated tungsten-based hot cathode of this embodiment uses a tungsten-osmium alloy cathode layer, and a grid is added to the surface of the hot cathode to adjust the surface emission of the hot cathode. The grid uses a ring or Mesh structure, the grid is isolated from the graphene layer 1 by an insulating dielectric layer or vacuum. By adjusting the voltage of the grid, the emission capability of the cathode can be adjusted.
Embodiment 3
[0039]The only difference from Example 1 is that the graphene-coated tungsten-based hot cathode of this embodiment uses a carbon-doped tungsten cathode layer, and the graphene layer 1 is a double-layer graphene; during the preparation process, wet transfer is used. The method realizes the graphene layer on the tungsten substrate.
PUM
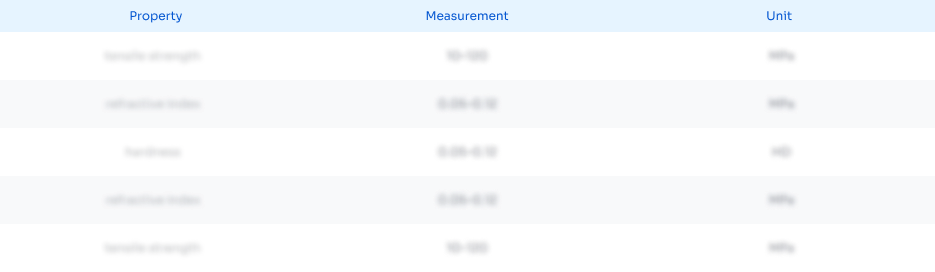
Abstract
Description
Claims
Application Information

- R&D
- Intellectual Property
- Life Sciences
- Materials
- Tech Scout
- Unparalleled Data Quality
- Higher Quality Content
- 60% Fewer Hallucinations
Browse by: Latest US Patents, China's latest patents, Technical Efficacy Thesaurus, Application Domain, Technology Topic, Popular Technical Reports.
© 2025 PatSnap. All rights reserved.Legal|Privacy policy|Modern Slavery Act Transparency Statement|Sitemap|About US| Contact US: help@patsnap.com