Numerical prediction method for two-phase flow and phase change process in gas-containing hydraulic turbine
A numerical prediction and phase flow technology, applied in CAD numerical modeling, electrical digital data processing, instruments, etc., can solve problems such as difficult prediction, difficulty in describing the fine structure of phase interface, and description distortion
- Summary
- Abstract
- Description
- Claims
- Application Information
AI Technical Summary
Problems solved by technology
Method used
Image
Examples
Embodiment Construction
[0055] The present invention will be further described below in conjunction with the accompanying drawings.
[0056] Such as figure 1 A numerical prediction method for two-phase flow and phase change process in a gas-containing hydraulic turbine is shown, including the following steps: Step S1: Establish a small-scale discrete bubble model, an optimized continuous interface capture method, and the conversion of discrete bubbles and continuous interfaces method;
[0057] Step S2: Divide the calculation domain grid and determine the large-scale phase interface and small-scale phase interface in the two-phase flow according to the set size, and obtain the physical parameters of different media in the two-phase flow and the physical parameters of discrete particles; The scale is that the size of the phase interface is greater than or equal to the grid size of the calculation domain, and the small scale is that the size of the phase interface is smaller than the grid size of the c...
PUM
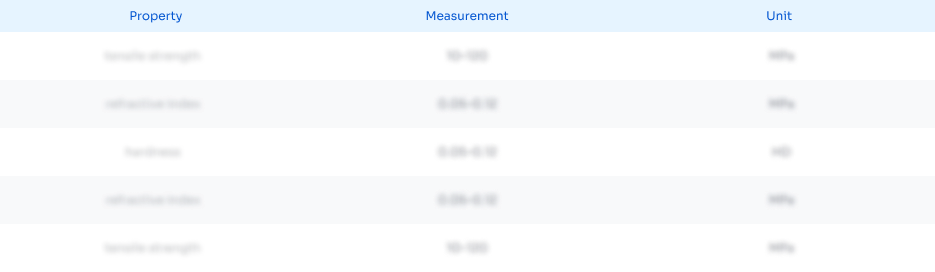
Abstract
Description
Claims
Application Information

- R&D
- Intellectual Property
- Life Sciences
- Materials
- Tech Scout
- Unparalleled Data Quality
- Higher Quality Content
- 60% Fewer Hallucinations
Browse by: Latest US Patents, China's latest patents, Technical Efficacy Thesaurus, Application Domain, Technology Topic, Popular Technical Reports.
© 2025 PatSnap. All rights reserved.Legal|Privacy policy|Modern Slavery Act Transparency Statement|Sitemap|About US| Contact US: help@patsnap.com