A low-temperature pyrolysis method and system for waste catalysts in residual oil hydrogenation
A waste catalyst and low-temperature pyrolysis technology, applied in the chemical industry, can solve the problems of increased production cost, high energy consumption, environmental pollution, etc., and achieve the effect of reducing the sealing pressure
- Summary
- Abstract
- Description
- Claims
- Application Information
AI Technical Summary
Problems solved by technology
Method used
Image
Examples
Embodiment 1
[0094] 1. Experimental raw materials
[0095] 1. Raw materials:
[0096] The waste catalyst for hydrogenation of residual oil comes from an oil refinery. The components of the waste catalyst for hydrogenation of residual oil and their respective percentages are: alumina 65%, molybdenum 4%, vanadium pentoxide 15%, oil 15%, The physical and chemical characteristics of the waste catalyst for hydrogenation of residual oil are: diesel odor, black clover-shaped solid.
[0097] 2. Equipment:
[0098] Feed screw conveyor (1), first rotary kiln (2), second rotary kiln (3), kiln tail sealing cover (4), discharge screw conveyor (5), cooling water inlet pipe (6), Cooling water outlet pipe (7), receiving barrel (8), surface cooling pipe (9), oil-water separator (10), oil tank (11), water-sealed flame-retardant tank (12), water ring vacuum pump (13) , circulating water tank (14), tail gas pipeline (15), tail gas water seal tank (16), kiln head sealing cover (17), oil and gas pipeline (18...
Embodiment 2
[0113] 1. Experimental raw materials
[0114] 1. Raw materials:
[0115] The waste catalyst for hydrogenation of residual oil comes from an oil refinery. The components of the waste catalyst for hydrogenation of residual oil and their respective percentages are: alumina 65%, molybdenum 4%, vanadium pentoxide 15%, oil 15%, The physical and chemical characteristics of the waste catalyst for hydrogenation of residual oil are: diesel odor, black clover-shaped solid.
[0116] 2. Equipment:
[0117] Feed screw conveyor (1), first rotary kiln (2), second rotary kiln (3), kiln tail sealing cover (4), discharge screw conveyor (5), cooling water inlet pipe (6), Cooling water outlet pipe (7), receiving barrel (8), surface cooling pipe (9), oil-water separator (10), oil tank (11), water-sealed flame-retardant tank (12), water ring vacuum pump (13) , circulating water tank (14), tail gas pipeline (15), tail gas water seal tank (16), kiln head sealing cover (17), oil and gas pipeline (18...
Embodiment 3
[0132] 1. Experimental raw materials
[0133] 1. Raw materials:
[0134] The waste catalyst for hydrogenation of residual oil comes from an oil refinery. The components of the waste catalyst for hydrogenation of residual oil and their respective percentages are: alumina 65%, molybdenum 4%, vanadium pentoxide 15%, oil 15%, The physical and chemical characteristics of the waste catalyst for hydrogenation of residual oil are: diesel odor, black clover-shaped solid.
[0135] 2. Equipment:
[0136] Feed screw conveyor (1), first rotary kiln (2), second rotary kiln (3), kiln tail sealing cover (4), discharge screw conveyor (5), cooling water inlet pipe (6), Cooling water outlet pipe (7), receiving barrel (8), surface cooling pipe (9), oil-water separator (10), oil tank (11), water-sealed flame-retardant tank (12), water ring vacuum pump (13) , circulating water tank (14), tail gas pipeline (15), tail gas water seal tank (16), kiln head sealing cover (17), oil and gas pipeline (18...
PUM
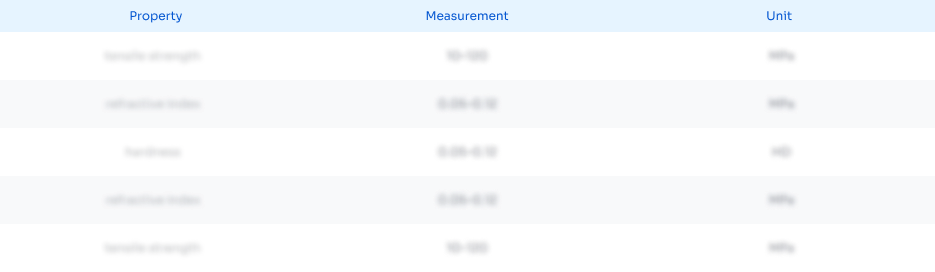
Abstract
Description
Claims
Application Information

- R&D
- Intellectual Property
- Life Sciences
- Materials
- Tech Scout
- Unparalleled Data Quality
- Higher Quality Content
- 60% Fewer Hallucinations
Browse by: Latest US Patents, China's latest patents, Technical Efficacy Thesaurus, Application Domain, Technology Topic, Popular Technical Reports.
© 2025 PatSnap. All rights reserved.Legal|Privacy policy|Modern Slavery Act Transparency Statement|Sitemap|About US| Contact US: help@patsnap.com