Thermal cracking comprehensive utilization method for iron and steel industry solid waste and hazardous waste resources
A technology of thermal cracking in the iron and steel industry, which is applied in the fields of thermal cracking, solid waste and hazardous waste treatment, and the iron and steel industry. The effect of saving investment in environmental protection
- Summary
- Abstract
- Description
- Claims
- Application Information
AI Technical Summary
Problems solved by technology
Method used
Image
Examples
Embodiment 1
[0042] After pretreatment of 100 tons of waste cloth bags, thermal cracking treatment is carried out in the continuous thermal cracking host, and the final temperature of cracking is set between 300-600°C, and the cracking reaction time is set between 0.5-2h;
[0043] The high-temperature gas generated by the pyrolysis reaction is cooled by the oil-gas separation cooler to obtain two products: combustible gas and fuel oil; the combustible gas is desulfurized by the desulfurization device and then sent to the gas cabinet, and part of the combustible gas is passed to the combustion heating device. Provide high-temperature flue gas for the pyrolysis main engine, and the surplus combustible gas is used for power generation, rotary kiln, and merged into the gas pipeline network; fuel oil is stored for export;
[0044] The solid product obtained from the thermal cracking reaction is sent to the ash slag bin through the discharge system, and is used as raw material for the solid waste t...
Embodiment 2
[0048] After pretreatment of 100 tons of oily sludge, thermal cracking treatment is carried out in the main engine of continuous thermal cracking, and the final temperature of cracking is set between 200-500°C, and the cracking reaction time is set between 0.5-2h; finally The fuel oil is about 70 tons, and its combustion value is about 40000kj / kg; the ash residue is about 2 tons, of which the C content is about 60%, and the TFe content is about 20%; the obtained combustible gas combustion value is about 14000KJ / Nm 3 , in addition to the fuel required for the combustion of the heating device in this system, it can also generate electricity of about 30,000kW·h.
[0049] Its processing method route is with embodiment 1.
Embodiment 3
[0051] After pretreatment of 100 tons of tar residue, thermal cracking treatment is carried out in the main engine of continuous thermal cracking, and the final temperature of cracking is set between 300-600°C, and the cracking reaction time is set between 0.5-2h; the final fuel About 30 tons of oil, its combustion value is about 40000kj / kg; about 35 tons of ash, of which the C content is about 75%; the combustion value of combustible gas obtained from cracking is about 7500Kj / Nm 3 , in addition to the fuel required for the combustion of the heating device in this system, it can also generate electricity of about 10000kW·h.
[0052] Its processing method route is with embodiment 1.
PUM
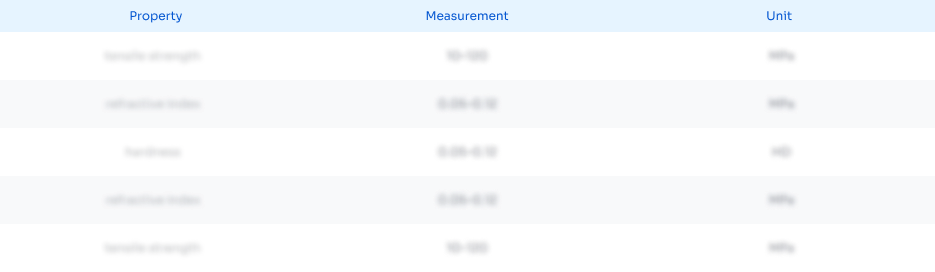
Abstract
Description
Claims
Application Information

- Generate Ideas
- Intellectual Property
- Life Sciences
- Materials
- Tech Scout
- Unparalleled Data Quality
- Higher Quality Content
- 60% Fewer Hallucinations
Browse by: Latest US Patents, China's latest patents, Technical Efficacy Thesaurus, Application Domain, Technology Topic, Popular Technical Reports.
© 2025 PatSnap. All rights reserved.Legal|Privacy policy|Modern Slavery Act Transparency Statement|Sitemap|About US| Contact US: help@patsnap.com