Magnesium slow-release bone cement with self-curing function and preparation method thereof
A bone cement, self-curing technology, applied in medical science, tissue regeneration, prosthesis, etc., can solve the problems of fast magnesium degradation, poor bone ability, difficult to control the slow release rate of magnesium, etc., to avoid bone cement to promote bone. Poor ability, good biocompatibility, avoiding the effect of calcium phosphate bone cement disintegration
- Summary
- Abstract
- Description
- Claims
- Application Information
AI Technical Summary
Problems solved by technology
Method used
Image
Examples
Embodiment 1
[0036] The magnesium slow-release bone cement with self-curing function provided in Example 1 is made by mixing and solidifying powder and water according to the ratio of mass to volume of 1g:0.5ml. The powder is calculated by mass percentage and includes the following raw materials Components: 2.86g of tetracalcium phosphate, 0.8g of calcium hydrogen phosphate, and 0.34g of magnesium phosphate; the aqueous solution is calculated by mass percentage, and includes the following raw materials: 1g of citric acid, 1g of polyvinylpyrrolidone, and 8ml of deionized water.
[0037] The magnesium slow-release bone cement with self-curing function provided in Example 1 is realized through the following steps:
[0038] S1. Preparation of powder: Weigh 2.92g of tetracalcium phosphate, 1.08g of calcium hydrogen phosphate, and 0.1g of magnesium phosphate in sequence, stir and mix thoroughly to obtain powder;
[0039] S2. Preparation of water preparation: Measure 8ml of deionized water, weigh...
Embodiment 2
[0042] A magnesium slow-release bone cement with self-curing function provided in Example 2 is made by mixing and solidifying powder and water according to the ratio of mass to volume of 1g:0.55ml. The powder is calculated by mass percentage and includes the following raw materials Components: 2.86g of tetracalcium phosphate, 0.8g of calcium hydrogen phosphate, and 0.3g of magnesium hydrogen phosphate; the aqueous solution is calculated by mass percentage, and includes the following raw materials: 1.5g of citric acid, 0.8g of polyvinylpyrrolidone, and 7.7ml of deionized water.
[0043]The magnesium slow-release bone cement with self-curing function provided in Example 2 is realized through the following steps:
[0044] S1. Preparation of powder: Weigh 2.86g of tetracalcium phosphate, 0.8g of calcium hydrogen phosphate, and 0.3g of magnesium hydrogen phosphate in sequence, stir and mix well to obtain powder;
[0045] S2. Preparation of water agent: Measure 7.7ml of deionized wa...
Embodiment 3
[0048] The magnesium slow-release bone cement with self-curing function provided in Example 3 is made by mixing and solidifying powder and water according to the ratio of mass to volume of 1g:1ml. The powder is calculated by mass percentage and includes the following raw material groups Composition: 2.86g of tetracalcium phosphate, 0.8g of calcium hydrogen phosphate, 0.3g of magnesium hydrogen phosphate; the aqueous solution is calculated by mass percentage, and includes the following raw materials: 1.5g of citric acid, 0.8g of polyvinylpyrrolidone, and 7.7ml of deionized water.
[0049] The magnesium slow-release bone cement with self-curing function provided in Example 3 is realized through the following steps:
[0050] S1. Preparation of powder: Weigh 2.86g of tetracalcium phosphate, 0.8g of calcium hydrogen phosphate, and 0.3g of magnesium hydrogen phosphate in sequence, stir and mix well to obtain powder;
[0051] S2. Preparation of water agent: Measure 7.7ml of deionized...
PUM
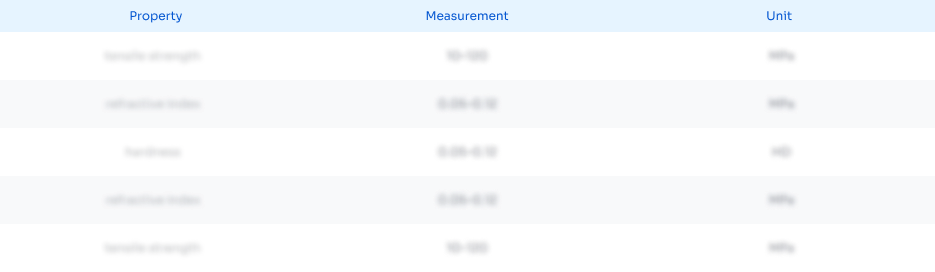
Abstract
Description
Claims
Application Information

- R&D
- Intellectual Property
- Life Sciences
- Materials
- Tech Scout
- Unparalleled Data Quality
- Higher Quality Content
- 60% Fewer Hallucinations
Browse by: Latest US Patents, China's latest patents, Technical Efficacy Thesaurus, Application Domain, Technology Topic, Popular Technical Reports.
© 2025 PatSnap. All rights reserved.Legal|Privacy policy|Modern Slavery Act Transparency Statement|Sitemap|About US| Contact US: help@patsnap.com