An autonomous calibration method for manipulator based on vision measurement
A calibration method and visual measurement technology, applied to manipulators, program-controlled manipulators, manufacturing tools, etc., to achieve high efficiency and low cost
- Summary
- Abstract
- Description
- Claims
- Application Information
AI Technical Summary
Problems solved by technology
Method used
Image
Examples
Embodiment 1
[0112] refer to Figure 1-8 , an autonomous calibration method for a robotic arm based on visual measurement, comprising the following steps:
[0113] Step 1: Build an unsteady multi-sensor manipulator vision system;
[0114] Taking the life science glove box robotic arm of China Space Station as the research platform, in order to obtain higher positioning accuracy and improve the fit between the model and the actual geometric configuration of the robotic arm, a more stringent improved DH model was established, and a Group of angles, to represent the error angle of the connecting rod rotating around the y-axis, preferably, all angle values are zero; axis 1 is an arc guideway, in the mechanical model, it is abstracted as a rotation axis with a virtual link, the The length of the connecting rod is equal to the radius of the arc guide rail. During the preparation process, the positions of the three two-dimensional code marking points in the base coordinate system are respectiv...
PUM
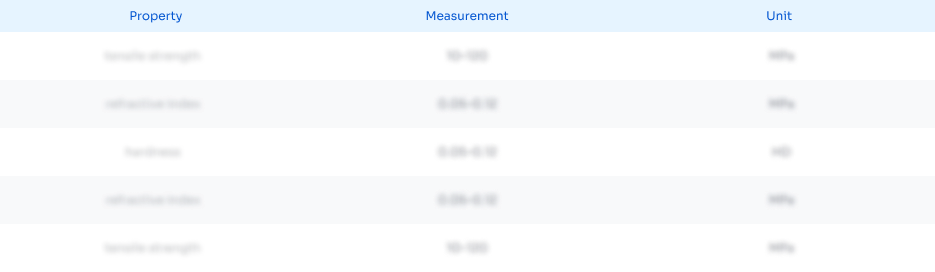
Abstract
Description
Claims
Application Information

- Generate Ideas
- Intellectual Property
- Life Sciences
- Materials
- Tech Scout
- Unparalleled Data Quality
- Higher Quality Content
- 60% Fewer Hallucinations
Browse by: Latest US Patents, China's latest patents, Technical Efficacy Thesaurus, Application Domain, Technology Topic, Popular Technical Reports.
© 2025 PatSnap. All rights reserved.Legal|Privacy policy|Modern Slavery Act Transparency Statement|Sitemap|About US| Contact US: help@patsnap.com