Method for refining magnesite
A magnesite and concentrate technology, applied in solid separation, flotation, etc., to achieve the effect of expanding the cut-off grade, facilitating comprehensive utilization, and improving separation performance
- Summary
- Abstract
- Description
- Claims
- Application Information
AI Technical Summary
Problems solved by technology
Method used
Image
Examples
Embodiment 1
[0036] Example 1, refer to figure 1 , a method for refining magnesite, its steps are:
[0037] ①The raw ore is crushed and wet-milled to make pulp with a weight concentration of 30%;
[0038] 2. The ore pulp enters the mixing barrel, and the slurry is fully adjusted after adding the collector I, and then enters the flotation machine for flotation, and the foam product is tailings I;
[0039] 3. The pulp enters the mixing tank, add regulator I and regulator II to fully adjust the slurry, enter the next mixing tank, add collector III to fully adjust the slurry, and enter the flotation machine for flotation, and the product in the tank is tailings II;
[0040] ④The foam product enters the mixing tank, and adjuster II is added to fully adjust the slurry, and then enter the flotation machine for flotation, and the product in the tank is medium ore;
[0041] ⑤ Repeat step ④ for 5 times to obtain the intermediate ore and final foam product of each stage in turn, and the final foam ...
Embodiment 2
[0047] Example 2, refer to figure 1 , a method of refining magnesite experiment one:
[0048] A magnesite ore in Liaoning, the raw ore is composed of MgO content of 45.51%, CaO content of 1.28%, and silicate content of 1.90%. After crushing and grinding, it is made into pulp with a concentration of 30%. %, collector I consumption is that 0.6kg / T carries out slurry mixing, obtains tailings I after flotation;
[0049] The dosage of adjuster I is 2.0kg / T, the dosage of adjuster II is 10.0kg / T for sizing, and the dosage of collector III is 1.0kg / T for sizing, and the product in the tank is tailings II after flotation;
[0050] For foam selection, the dosage of Regulator II is 1.0kg / T to sizing the foam, and the product in the tank after flotation is medium ore I; for foam selection, the dosage of Regulator II is 1.0kg / T to sizing the foam, After flotation, the product in the tank is medium ore II, and the foam product is magnesite concentrate. The concentrate composition is 46.8...
Embodiment 3
[0056] Example 3, refer to figure 1 , a method for refining magnesite, its steps are:
[0057] ①The raw ore is crushed and wet-milled into pulp with a weight concentration of 30%.
[0058] ②The ore pulp enters the mixing barrel, and after adding the collector I, the slurry is fully adjusted, and then enters the flotation machine for flotation, and the foam product is tailings I,
[0059] ③The pulp enters the mixing tank, add the adjusting agent I to fully adjust the pulp, enter the next mixing tank, add the collector II to fully adjust the pulp, and enter the flotation machine for flotation. The foam product is tailings II,
[0060] ④The pulp enters the mixing tank, and adjuster II is added to fully adjust the pulp. Then it enters the next mixing tank and collector III is added to fully adjust the pulp, and then enters the flotation machine for flotation. The product in the tank is tailings III.
[0061] ⑤ The foam product enters the mixing tank, and adjuster II is added to ...
PUM
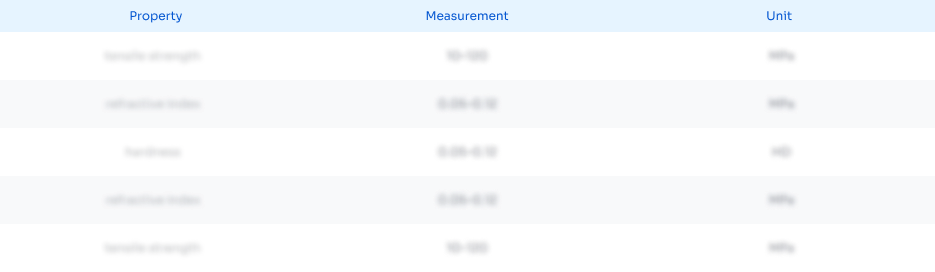
Abstract
Description
Claims
Application Information

- R&D
- Intellectual Property
- Life Sciences
- Materials
- Tech Scout
- Unparalleled Data Quality
- Higher Quality Content
- 60% Fewer Hallucinations
Browse by: Latest US Patents, China's latest patents, Technical Efficacy Thesaurus, Application Domain, Technology Topic, Popular Technical Reports.
© 2025 PatSnap. All rights reserved.Legal|Privacy policy|Modern Slavery Act Transparency Statement|Sitemap|About US| Contact US: help@patsnap.com