Hydrogenation catalyst compositions and their use for hydrogenation of nitrile rubber
A technology of hydrogenation catalysts and compositions, applied in physical/chemical process catalysts, organic compound/hydride/coordination complex catalysts, catalytic reactions, etc.
- Summary
- Abstract
- Description
- Claims
- Application Information
AI Technical Summary
Problems solved by technology
Method used
Image
Examples
Embodiment 1
[0346] Example 1*: (comparative example, use catalyst (1), in No In the case of EVE preprocessing)
[0347] Catalyst (1 ) (10.8 mg) was dissolved in 15 mL of degassed MCB in a flask. 36g with nitrogen The solution of 3431F in 247.5g MCB ( 3431F at a concentration of 15 wt.%) was bubbled in a 600 mL Parr autoclave for 30 minutes and then heated to 138°C. The catalyst solution in the flask was transferred into the reactor via syringe. The hydrogenation was carried out at a hydrogen pressure of 8.27 MPa and a stirring speed of 800 rpm. Samples were taken from the reactor at regular intervals for FT-IR analysis to determine the degree of hydrogenation. After 5 hours of hydrogenation, the degree of hydrogenation reached 85.0%. Final molecular weight and PDI are: Mn=59,471 g / mol, Mw=178,552 g / mol, PDI=3.
Embodiment 2
[0348] Example 2: (embodiment of the present invention: use catalyst (1), in use In the case of EVE as a co-catalyst)
[0349] Catalyst (1 ) (10.8 mg) was dissolved in 15 g of degassed MCB in a flask. Ethyl vinyl ether (0.375 mL) was injected into the flask and the solution was stirred at 20 °C for 12 hours. 36g with nitrogen The solution of 3431F in 247.5g MCB ( 3431F at a concentration of 15 wt.%) was bubbled in a 600 mL Parr autoclave for 30 minutes, and then heated to 138°C. The catalyst solution in the flask was transferred into the reactor via syringe. The hydrogenation was carried out at a hydrogen pressure of 8.27 MPa and a stirring speed of 800 rpm. Samples were taken from the reactor at regular intervals for FT-IR analysis to determine the degree of hydrogenation. After 5 hours of hydrogenation, the degree of hydrogenation reached 98.1%. Final molecular weight and PDI are: Mn = 64,283 g / mol, Mw = 186,381 g / mol, PDI = 2.9.
Embodiment 3
[0350] Example 3: (embodiment of the present invention: use catalyst (2), in use In the case of EVE as a co-catalyst)
[0351] Catalyst (2) (10.8 mg) was dissolved in 15 g of degassed MCB in a flask. Ethyl vinyl ether (0.375 mL) was injected into the flask and the solution was stirred for 12 hours. 36g with nitrogen The solution of 3431F in 247.5g MCB ( 3431F at a concentration of 15 wt.%) was bubbled in a 600 mL Parr autoclave for 30 minutes and then heated to 138°C. The catalyst solution in the flask was transferred into the reactor via syringe. The hydrogenation was carried out at a hydrogen pressure of 8.27 MPa and a stirring speed of 800 rpm. Samples were taken from the reactor at regular intervals for FT-IR analysis to determine the degree of hydrogenation. After 3 hours of hydrogenation, the degree of hydrogenation reached 98.9%. Final molecular weight and PDI are: Mn = 57,556 g / mol, Mw = 170,413 g / mol, PDI = 2.95.
PUM
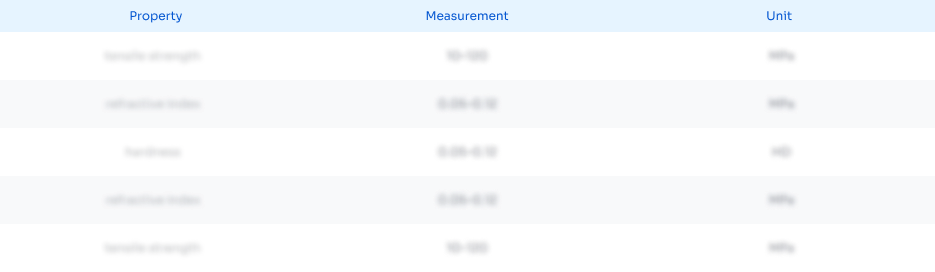
Abstract
Description
Claims
Application Information

- R&D
- Intellectual Property
- Life Sciences
- Materials
- Tech Scout
- Unparalleled Data Quality
- Higher Quality Content
- 60% Fewer Hallucinations
Browse by: Latest US Patents, China's latest patents, Technical Efficacy Thesaurus, Application Domain, Technology Topic, Popular Technical Reports.
© 2025 PatSnap. All rights reserved.Legal|Privacy policy|Modern Slavery Act Transparency Statement|Sitemap|About US| Contact US: help@patsnap.com