Multipurpose transmission system and construction scheme thereof
A transmission system and multi-purpose technology, applied in the aerospace field, can solve the problems of the airship airbag inflation rate and skin bearing capacity reaching the limit, the pressure difference between the inside and outside of the airship airbag increasing, etc., achieving easy static hovering and solving slow steering action , the effect of improving efficiency
- Summary
- Abstract
- Description
- Claims
- Application Information
AI Technical Summary
Problems solved by technology
Method used
Image
Examples
Embodiment 1
[0044] Embodiment one. Leave the factory.
[0045] After all components of the space-to-ground transmission system are manufactured and passed the test, the manufacturing base will be moved to the space launch ground base (if the manufacturing base has good conditions in all aspects, it can also be directly transformed into a space launch ground base). In order to facilitate air maneuvering flight, the system will be temporarily combined into two sets of autonomous maneuvering aerostats, one set is based on the super-floater (1), and the other is based on the giant aerostat (4). as the subject. First, temporarily install and fix components such as the functional module, the mission cabin, the cable car (8), the mooring transmission cable upper section (712) and the lift overload protection cable (73) that are planned to be carried in sequence. , the functional areas, the space launch plaza (21), and the control platform (3) that are stored on the superfloater (1); mooring the...
Embodiment 2
[0046] Embodiment 2. The base is assembled and lifted off.
[0047] After the space-to-ground transmission system leaves the factory, it flies to the space above the space launch ground base through low-to-medium altitude flight. The giant floater (4) maneuvers at a low speed to directly above the predetermined installation position of the triangular wind-resistant and tension-resistant anchor station (62) and keeps hovering. After the spare cable car (8) is loaded with the hollow combination unit (63) of the triangular wind-resistant and tension-resistant anchor station (62) in the transfer cabin, it moves to the passage shaft (43) through a special slideway facility. )Inside. The strong magnetic clutch (8113) on the traveling device (811) of the cable car is separated, the rotating surface (8171) of the hanger is opened, and the traveling device (811) is driven to deflect, and the guide wheel device (833) is opened similarly. The mooring cable lower section (711) enters th...
Embodiment 3
[0048] Embodiment three. Space launch.
[0049] After the space-ground transmission system receives a space launch mission in the standby state, it will take corresponding operation steps depending on the mission type. Since the space launch involved in the present invention starts at an altitude of 30--50km and above the adjacent space, the thick and heavy surface atmosphere is avoided. The thin atmosphere makes the rocket suffer from little resistance, and at the same time greatly improves the efficiency of the rocket engine. Therefore, compared with the traditional ground rocket launching, the present invention can greatly reduce the size of the rocket shell, the size of the engine, and the amount of fuel needed to complete the same load launch task, and the rocket with the same specification can bear a larger launch load.
[0050]When the launch task is a small and medium-sized satellite in low and medium orbits, the total weight of the satellite and the launch vehicle (2...
PUM
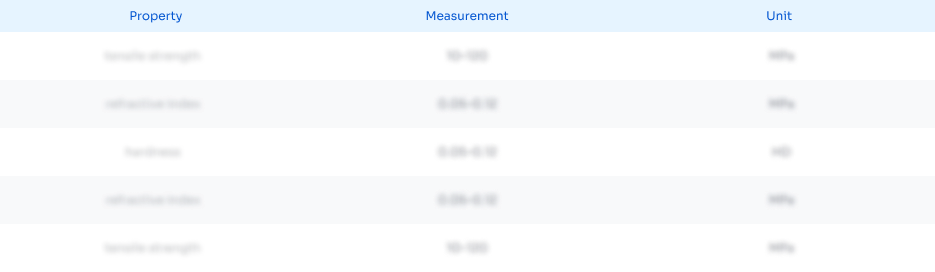
Abstract
Description
Claims
Application Information

- R&D
- Intellectual Property
- Life Sciences
- Materials
- Tech Scout
- Unparalleled Data Quality
- Higher Quality Content
- 60% Fewer Hallucinations
Browse by: Latest US Patents, China's latest patents, Technical Efficacy Thesaurus, Application Domain, Technology Topic, Popular Technical Reports.
© 2025 PatSnap. All rights reserved.Legal|Privacy policy|Modern Slavery Act Transparency Statement|Sitemap|About US| Contact US: help@patsnap.com