High-energy-consumption-density torsional eddy current damping device and damping system
A technology of eddy current damping and damping system, which is applied in the direction of springs, magnetic springs, springs/shock absorbers, etc., can solve the problems of low energy consumption density of eddy current damping and cannot adapt to high energy consumption density, and achieve structural vibration suppression, The effect of increasing energy consumption density
- Summary
- Abstract
- Description
- Claims
- Application Information
AI Technical Summary
Problems solved by technology
Method used
Image
Examples
Embodiment 1
[0037] Such as Figure 1-3 As shown, a high energy consumption density torsional eddy current damping device described in this embodiment includes at least one stage of speed-up gear set 11, and also includes conductor tubes 6 that are rotatably matched with each other and magnets that are staggered along the circular direction. 7. The output end of the speed-up gear set 11 is connected to the conductor tube 6, and the speed-up gear set 11 can drive the conductor tube 6 to rotate relative to the magnets 7 arranged staggered along the circular direction. The conductor pipe 6 is sheathed on the outside of the magnets 7 arranged staggered along the circular direction, and there is a gap between the conductor pipe 6 and the magnets 7 arranged staggered along the circular direction.
[0038]Specifically, the speed-up gear set 11 is a planetary gear mechanism, and the speed-up gear set 11 includes a planet carrier 4, a planetary gear 2, a sun gear 1 and an internal gear 3, and the m...
Embodiment 2
[0058] Such as Figure 1-4 As shown, a kind of damping system described in this embodiment includes the structure to be vibrated 14 and the high energy consumption density torsional eddy current damping device as described in Embodiment 1, the planet carrier 4 and the structure to be vibrated 14 is connected, and the internal gear 3 is connected with the structure 14 to be vibrated.
[0059] When the to-be-vibrated structure 14 generates torsional motion due to vibration or impact, it can transmit the torsional motion to the planet carrier 4, and through the speed-up effect of the planetary gear mechanism, the sun gear 1 will accelerate to rotate, thereby increasing the relative speed of the conductor tube 6 along the ring. The rotation speed of the magnets 7 arranged in a staggered direction, the conductor tube 6 moves relative to the magnets 7 arranged in a staggered direction in the ring direction in the magnetic field of the magnets 7 arranged in a staggered direction in t...
PUM
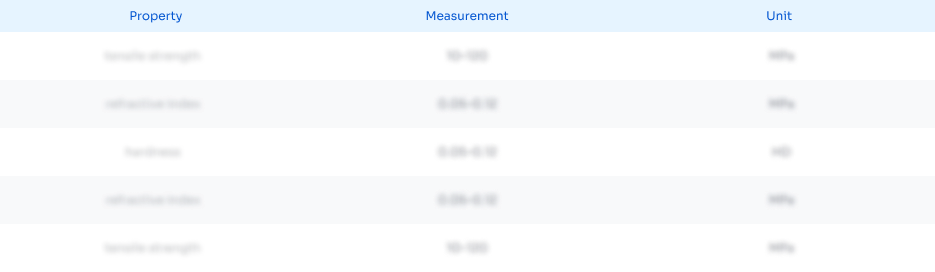
Abstract
Description
Claims
Application Information

- R&D
- Intellectual Property
- Life Sciences
- Materials
- Tech Scout
- Unparalleled Data Quality
- Higher Quality Content
- 60% Fewer Hallucinations
Browse by: Latest US Patents, China's latest patents, Technical Efficacy Thesaurus, Application Domain, Technology Topic, Popular Technical Reports.
© 2025 PatSnap. All rights reserved.Legal|Privacy policy|Modern Slavery Act Transparency Statement|Sitemap|About US| Contact US: help@patsnap.com