Melt-blown fabric hydro electret production line
A technology of melt-blown cloth and production line, which is applied in spraying/spraying textile material treatment, processing textile material carrier, removing liquid/gas/steam, etc., and can solve problems such as roughness of melt-blown cloth, less electret, and high risk factor , to achieve the effect of preventing offset and loosening
- Summary
- Abstract
- Description
- Claims
- Application Information
AI Technical Summary
Problems solved by technology
Method used
Image
Examples
specific Embodiment approach 1
[0040] Such as Figure 1-13 As shown, the meltblown water electret production line includes a driving mechanism 1, an unwinding mechanism 2, a leading fabric guiding mechanism 3, an electret box 4, a spunlace electret mechanism 5, a pressure regulating mechanism 6, a rolling mechanism 7, and a return water Collecting box 8, rear fabric guide mechanism 9, drying box 10, hot air blower 11, winding mechanism 12 and base 13, the driving mechanism 1 is connected on the described unwinding mechanism 2, and the driving mechanism 1 is connected to the described The unwinding mechanism 2; the unwinding mechanism 2, the front cloth guide mechanism 3, the electret box 4, the rear cloth guide mechanism 9, the drying box 10 and the winding mechanism 12 are installed on the base 13 in sequence from front to back; The front and rear ends of the inside of the electret box 4 are respectively connected to the spunlace electret mechanism 5 and the rolling mechanism 7; the pressure regulating mec...
specific Embodiment approach 2
[0043] Such as Figure 1-13 As shown, the unwinding mechanism 2 includes a side frame 201, a cloth roller 202, a side stop ring 203, a first gear 204, a second gear 205, a first pulley 206, a wheel shaft one 207 and a tension adjustment assembly; The two ends of the distribution roller 202 are plugged into the two front slots of the two side frames 201; the two ends of the distribution roller 202 are respectively fixed with a side stop ring 203, and the two side stop rings 203 are rolled and fitted on the two sides. On the outer side of the frame 201; one end of the distribution roller 202 is connected to the drive mechanism 1; the other end of the distribution roller 202 is fixedly connected to the first pulley 206 and the first gear 204, and the first gear 204 is meshed with the transmission connection The second gear 205; the second gear 205 and the first pulley 206 are all fixed on the wheel shaft one 207; the wheel shaft one 207 is rotatably connected to a side frame 201;...
specific Embodiment approach 3
[0046] Such as Figure 1-13 As shown, the drive mechanism 1 includes a servo motor 101 with a reducer, a drive shaft 102, a friction transmission wheel 103, a friction linkage wheel 104, a rotating plate 105 and a first screw 106; the servo motor 101 is fixed by a motor bracket Connected on a side frame 201; the output shaft of the servo motor 101 is connected to the drive shaft 102 through a coupling; the friction drive wheel 103 is slidingly fitted on the drive shaft 102; the top end of the drive shaft 102 is fixedly connected One end of the rotating plate 105; the other end of the rotating plate 105 is rotated and connected to the upper end of the first screw 106; the middle of the first screw 106 is threaded on the friction transmission wheel 103 to drive the The friction transmission wheel 103 slides up and down on the drive shaft 102 ; the friction transmission wheel 103 is vertically frictionally connected to the friction linkage wheel 104 ; the friction linkage wheel 1...
PUM
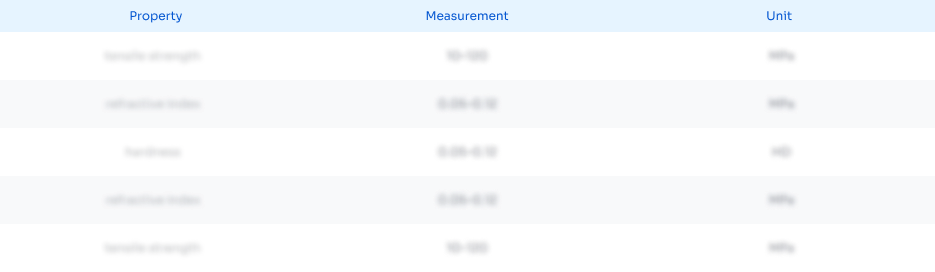
Abstract
Description
Claims
Application Information

- Generate Ideas
- Intellectual Property
- Life Sciences
- Materials
- Tech Scout
- Unparalleled Data Quality
- Higher Quality Content
- 60% Fewer Hallucinations
Browse by: Latest US Patents, China's latest patents, Technical Efficacy Thesaurus, Application Domain, Technology Topic, Popular Technical Reports.
© 2025 PatSnap. All rights reserved.Legal|Privacy policy|Modern Slavery Act Transparency Statement|Sitemap|About US| Contact US: help@patsnap.com