Novel energy-saving and consumption-reducing continuous cast tube annealing furnace system
An annealing furnace and casting tube technology, which is applied in the field of new energy-saving and consumption-reducing continuous cast tube annealing furnace system, can solve the problems of prolonging the furnace temperature increase time, environmental pollution, large energy consumption, etc., and achieve non-stop maintenance and reduce Production cost and the effect of protecting the production environment
- Summary
- Abstract
- Description
- Claims
- Application Information
AI Technical Summary
Problems solved by technology
Method used
Examples
Embodiment Construction
[0040] In order to make the technical problems solved by the present invention, the technical solutions adopted and the technical effects achieved clearer, the present invention will be further described in detail below in conjunction with the accompanying drawings and embodiments. It should be understood that the specific embodiments described here are only used to explain the present invention, but not to limit the present invention. In addition, it should be noted that, for the convenience of description, only parts related to the present invention are shown in the drawings but not all content.
[0041] figure 1 It is a structural schematic diagram of the new energy-saving and consumption-reducing continuous casting tube annealing furnace system provided by the present invention; figure 2 It is a top view of the new energy-saving and consumption-reducing continuous casting tube annealing furnace system provided by the present invention. Such as figure 1 , 2 As shown, t...
PUM
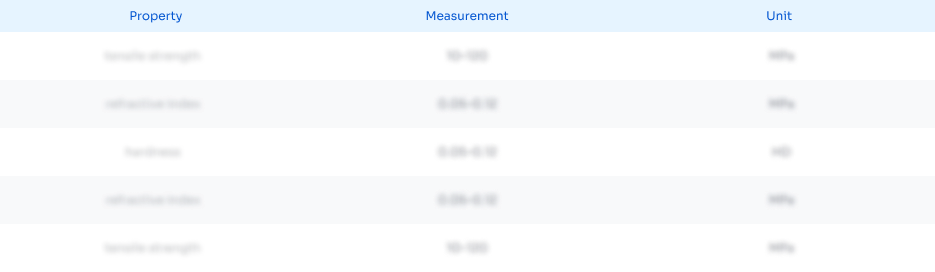
Abstract
Description
Claims
Application Information

- R&D
- Intellectual Property
- Life Sciences
- Materials
- Tech Scout
- Unparalleled Data Quality
- Higher Quality Content
- 60% Fewer Hallucinations
Browse by: Latest US Patents, China's latest patents, Technical Efficacy Thesaurus, Application Domain, Technology Topic, Popular Technical Reports.
© 2025 PatSnap. All rights reserved.Legal|Privacy policy|Modern Slavery Act Transparency Statement|Sitemap|About US| Contact US: help@patsnap.com