Heat-integrated process design for four carbon dioxide supplementing positions in methanol synthesis
A technology integrating methanol and process design, applied in the preparation of organic compounds, chemical industry, preparation of hydroxyl compounds, etc., can solve the problems of increasing energy consumption, increasing the water content of crude methanol, etc., to reduce the loss of effective energy, reduce emissions, and reduce energy consumption. consumption reduction effect
- Summary
- Abstract
- Description
- Claims
- Application Information
AI Technical Summary
Problems solved by technology
Method used
Image
Examples
Embodiment 1
[0047] The specific steps of a low-energy-consumption and high-environmental-friendly heat-integrated methanol synthesis method for four carbon-supplementing sites are as follows:
[0048] (1) Methane steam reforming (SMR)
[0049] The raw material 2500kmol / h natural gas is pretreated and divided into two paths, about 50% (volume fraction) of natural gas, 7500kmol / h water vapor and 25kmol / h added CO 2 -1 stream is heated to 669°C by the heater HEATER2 and mixed into the first-stage methane steam reformer. The heat required by HEATER2 is provided by the subsequent coolers C1 and C8, and all raw materials undergo methane steam reformation in the SMR high-temperature reformer at 890°C And water gas shift reaction. Then add a stream of 25kmol / h CO after the SMR reformer 2 flow (CO 2 -2) to adjust the hydrogen-carbon ratio.
[0050] (2) Carbon Dioxide Methane Reforming (DMR)
[0051] The raw material gas is transformed into H through step (1) 2 , CO, CO 2 and CH 4 The mixed...
Embodiment 2
[0059] A low-energy and high-environmental-friendly heat-integrated methanol synthesis process design method with four carbon-supplementing positions, same as implementation case 1, wherein:
[0060] In step (1), the raw material 2240kmol / h natural gas is pretreated and divided into two paths, about 50% (volume fraction) of natural gas, 6720kmol / h water vapor and 20kmol / h CO 2 The -1 stream is heated to 564°C by the heater HEATER2 and enters the SMR at 800°C for conversion. Then add a stream of 20kmol / h CO after the SMR reformer 2 flow (CO 2 -2) to adjust the hydrogen-carbon ratio.
[0061] In step (2), the mixed gas enters the gas-liquid separator FLASH1 to separate excess water after being cooled by the coolers C1~C6, and then the gas phase is heated to 339°C by the heaters H1 and H2, and then mixed with another natural gas and 600 kmol / h CO 2 -3 streams are mixed, heated to 496°C, enter the DMR at 700°C for reaction, and finally generate methanol synthesis gas.
[0062...
Embodiment 3
[0066] A low-energy and high-environmental-friendly heat-integrated methanol synthesis process design method with four carbon-supplementing positions, same as implementation case 1, wherein:
[0067] In step (1), the raw material 1680kmol / h natural gas is pretreated and divided into two paths, about 50% (volume fraction) of natural gas, 5040kmol / h water vapor and 15kmol / h CO 2 The -1 stream is heated to 503°C by the heater HEATER2 and enters the SMR at 750°C for conversion. Then add a stream of 15kmol / h CO after the SMR reformer 2 flow (CO 2 -2) to adjust the hydrogen-carbon ratio.
[0068] In step (2), the mixed gas enters the gas-liquid separator FLASH1 to separate excess water after being cooled by the coolers C1~C6, and then the gas phase is heated to 336°C by the heaters H1 and H2, and then mixed with another natural gas and 450kmol / h CO 2 -3 streams are mixed, heated to 493°C, enter the DMR at 650°C for reaction, and finally generate methanol synthesis gas.
[0069]...
PUM
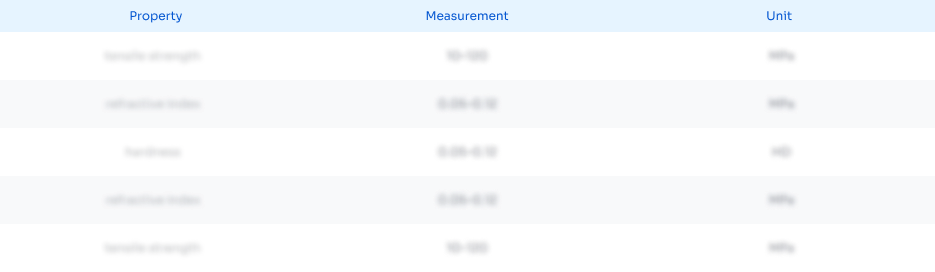
Abstract
Description
Claims
Application Information

- R&D
- Intellectual Property
- Life Sciences
- Materials
- Tech Scout
- Unparalleled Data Quality
- Higher Quality Content
- 60% Fewer Hallucinations
Browse by: Latest US Patents, China's latest patents, Technical Efficacy Thesaurus, Application Domain, Technology Topic, Popular Technical Reports.
© 2025 PatSnap. All rights reserved.Legal|Privacy policy|Modern Slavery Act Transparency Statement|Sitemap|About US| Contact US: help@patsnap.com