Three-dimensional network graphene-based tensile strain sensor and its preparation method
A graphene-based, tensile strain technology, applied in graphene, chemical instruments and methods, electric/magnetic solid deformation measurement, etc., can solve the problems of insufficient self-repair performance of sensors, internal damage of flexible materials, and decreased sensitivity of sensors. Achieve the effect of uniform compressive stress distribution, uniform tensile deformation and extended service life
- Summary
- Abstract
- Description
- Claims
- Application Information
AI Technical Summary
Problems solved by technology
Method used
Image
Examples
Embodiment 1
[0026] A three-dimensional network graphene-based tensile strain sensor, its preparation method comprising:
[0027] (1) Preparation of soft gel precursor:
[0028] Dissolve 5g of urea and 8g of formaldehyde in 50ml of water to obtain mixed solution A; dissolve vinyl polydimethylsiloxane, N-isopropylacrylamide, and vinylpyrrolidone in the solvent respectively to obtain a mass volume concentration of 8g / 100ml The solutions B, C, and D were mixed and reacted with the solutions A, B, C, and D according to the volume ratio of 1:2:1:1 to obtain the reaction product M, which is the soft gel precursor.
[0029] (2) Preparation of graphene with 3D network structure:
[0030] The nickel foam was cleaned sequentially with alcohol, acetone, and deionized water, and then dried with nitrogen gas. As a template for growing graphene with a 3D network structure, the cleaned and dried nickel foam was transferred to a chemical vapor deposition device, and the nickel foam was sprayed with metha...
Embodiment 2
[0037] A three-dimensional network graphene-based tensile strain sensor, its preparation method comprising:
[0038] (1) Preparation of soft gel precursor:
[0039] Dissolve 3g of urea and 7g of formaldehyde in 50ml of water to obtain a mixed solution A; dissolve vinyl polydimethylsiloxane, N-isopropylacrylamide, and vinylpyrrolidone in the solvent respectively to obtain a mass volume concentration of 6g / 100ml The solutions B, C, and D were mixed and reacted with the solutions A, B, C, and D according to the volume ratio of 1:2:1:1 to obtain the reaction product M, which is the soft gel precursor.
[0040] (2) Preparation of graphene with 3D network structure:
[0041] The nickel foam was cleaned sequentially with alcohol, acetone, and deionized water, and then dried with nitrogen gas. As a template for growing graphene with a 3D network structure, the cleaned and dried nickel foam was transferred to a chemical vapor deposition device, and the nickel foam was sprayed with met...
Embodiment 3
[0048] A three-dimensional network graphene-based tensile strain sensor, its preparation method comprising:
[0049] (1) Preparation of soft gel precursor:
[0050] Dissolve 3g of urea and 10g of formaldehyde in 50ml of water to obtain a mixed solution A; dissolve vinyl polydimethylsiloxane, N-isopropylacrylamide, and vinylpyrrolidone in the solvent respectively to obtain a mass volume concentration of 10g / 100ml The solutions B, C, and D were mixed and reacted with the solutions A, B, C, and D according to the volume ratio of 1:2:1:1 to obtain the reaction product M, which is the soft gel precursor.
[0051] (2) Preparation of graphene with 3D network structure:
[0052] The nickel foam was cleaned sequentially with alcohol, acetone, and deionized water, and then dried with nitrogen gas. As a template for growing graphene with a 3D network structure, the cleaned and dried nickel foam was transferred to a chemical vapor deposition device, and the nickel foam was sprayed with m...
PUM
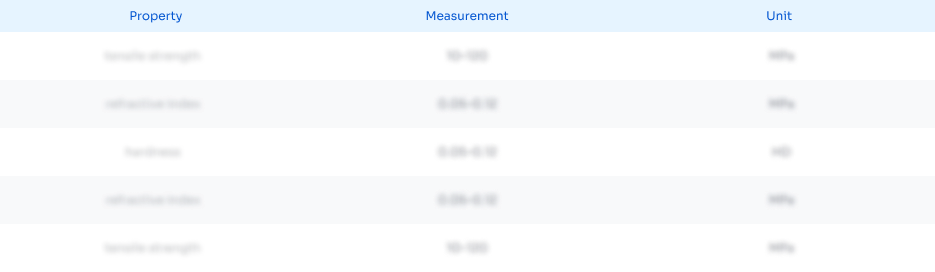
Abstract
Description
Claims
Application Information

- Generate Ideas
- Intellectual Property
- Life Sciences
- Materials
- Tech Scout
- Unparalleled Data Quality
- Higher Quality Content
- 60% Fewer Hallucinations
Browse by: Latest US Patents, China's latest patents, Technical Efficacy Thesaurus, Application Domain, Technology Topic, Popular Technical Reports.
© 2025 PatSnap. All rights reserved.Legal|Privacy policy|Modern Slavery Act Transparency Statement|Sitemap|About US| Contact US: help@patsnap.com