Atomization adding device and atomization adding method for neodymium iron boron magnetic powder mixture additive
A technology of adding devices and additives, which is applied to magnetic materials, magnetic objects, transportation and packaging, etc., can solve the problems of difficult actual flow control, difficult cleaning, and inconvenient cleaning, so as to avoid the decline of mechanical properties, improve the yield rate of magnets, Avoid the effect of degrading magnetic properties
- Summary
- Abstract
- Description
- Claims
- Application Information
AI Technical Summary
Problems solved by technology
Method used
Image
Examples
Embodiment 1
[0031] One can of powder before milling, 360kg, was atomized by the device of the present invention to add antioxidant, and then mixed in a three-dimensional mixer for 1.5 hours. During the milling process, 8 samples were taken to test the C content deviation.
Embodiment 2
[0033] The batch weight is 700kg. After pulverization, 2 cans of powder are put into the V-type mixer. The device of the present invention is used to atomize the feeding port of the V-type mixer and then mix the materials for 4 hours. When pressing, take 8 pieces in order. Powder samples were tested for C content deviation.
Embodiment 3
[0035] The batch weight is 700kg. After pulverization, 2 cans of powder are put into the V-type mixer, and the device of the present invention is used to atomize the feeding port of the V-type mixer and add lubricant. After mixing for 4 hours, the magnetic field is pressed to form, sinter, and Out of the furnace, 13 blanks were sampled from the corners, edge centers, and body centers (cuboid apex, edge center, and center) of the upper, middle, and lower layers in the furnace, and the C content deviation was tested.
PUM
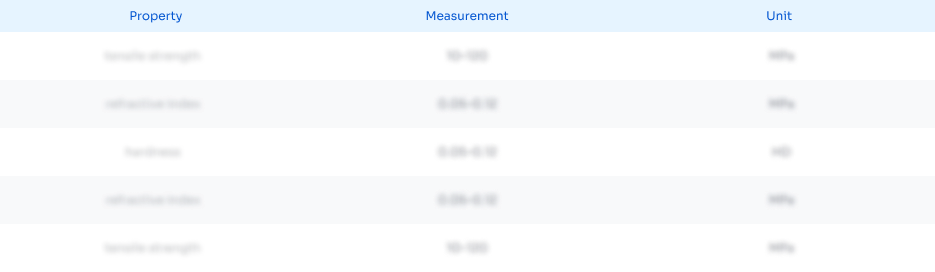
Abstract
Description
Claims
Application Information

- Generate Ideas
- Intellectual Property
- Life Sciences
- Materials
- Tech Scout
- Unparalleled Data Quality
- Higher Quality Content
- 60% Fewer Hallucinations
Browse by: Latest US Patents, China's latest patents, Technical Efficacy Thesaurus, Application Domain, Technology Topic, Popular Technical Reports.
© 2025 PatSnap. All rights reserved.Legal|Privacy policy|Modern Slavery Act Transparency Statement|Sitemap|About US| Contact US: help@patsnap.com