Method for recycling lithium iron phosphate batteries
A lithium iron phosphate battery, iron sulfate technology, applied in the direction of improving process efficiency, can solve problems such as high cost and large consumption of organic acids, and achieve the effects of reducing water consumption, reducing sewage discharge, and high lithium recovery rate
- Summary
- Abstract
- Description
- Claims
- Application Information
AI Technical Summary
Problems solved by technology
Method used
Examples
Embodiment 1
[0057] Manually disassemble the lithium iron phosphate battery, separate the positive electrode, negative electrode, diaphragm, and iron shell to obtain the battery positive electrode powder. The ferric nitrate and positive electrode powder were mixed and ball-milled, the ball-to-material ratio was 2:1, and the ball-milling time was 2 hours (30 minutes of ball milling, 30 minutes of shutdown). Wherein, the molar ratio of ferric nitrate to iron in the powder is 1:1. The mixed powder is passed through a 200-mesh sieve, and the undersize is taken. The oversize is returned to the previous step for re-ball milling; the undersize is roasted in an air atmosphere at a roasting temperature of 600°C for 2 hours. Crush the roasted product and leaching with deionized water, the ratio of solid to liquid is 1:3. Filter the mixed slurry, and the filtrate is used as the lithium sinking mother liquor. According to analysis and testing, under this condition, 99.1% of lithium can be effective...
Embodiment 2
[0059] Manually disassemble the lithium iron phosphate battery, separate the positive electrode, negative electrode, diaphragm, and iron shell to obtain the battery positive electrode powder. The ferric acetate and the positive electrode powder were mixed and ball-milled, the ball-to-material ratio was 3:2, and the ball-milling time was 2h (30min ball milling, 30min shutdown). Wherein, the molar ratio of iron acetate to iron in the powder is 1:1. The mixed powder is passed through a 200-mesh sieve, and the undersize is taken. The oversize is returned to the previous step for re-ball milling; the undersize is roasted in an air atmosphere at a roasting temperature of 550°C for 3 hours. Crush the roasted product and leaching with deionized water, the ratio of solid to liquid is 1:4. Filter the mixed slurry, and the filtrate is used as the lithium sinking mother liquor. Through analysis and testing, under this condition, the recovery rate of lithium is 99.5%.
Embodiment 3
[0061] Manually disassemble the lithium iron phosphate battery, separate the positive electrode, negative electrode, diaphragm, and iron shell to obtain the battery positive electrode powder. The ferric sulfate heptahydrate and the positive electrode powder were mixed and ball-milled, the ball-to-material ratio was 2:1, and the ball-milling time was 3 hours (30 minutes of ball milling, 30 minutes of shutdown). Wherein, the molar ratio of ferric sulfate heptahydrate to iron in the powder is 1:1. The mixed powder is passed through a 200-mesh sieve, and the undersize is taken. The oversize is returned to the previous step for re-ball milling; the undersize is roasted in an air atmosphere at a roasting temperature of 550°C for 4 hours. Crush the roasted product and leaching with deionized water, the solid-to-liquid ratio is 1:3.5. Filter the mixed slurry, and the filtrate is used as the lithium sinking mother liquor. Through analysis and testing, under this condition, the recov...
PUM
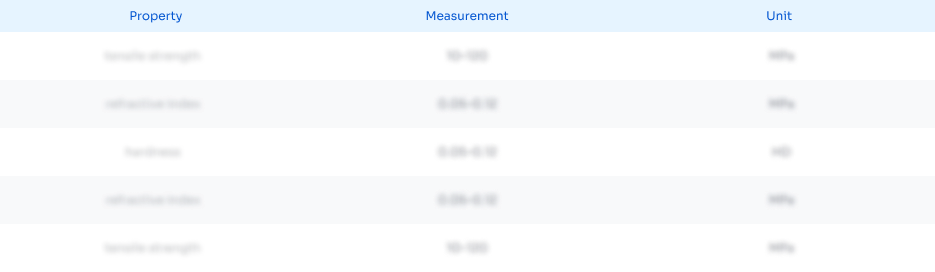
Abstract
Description
Claims
Application Information

- R&D
- Intellectual Property
- Life Sciences
- Materials
- Tech Scout
- Unparalleled Data Quality
- Higher Quality Content
- 60% Fewer Hallucinations
Browse by: Latest US Patents, China's latest patents, Technical Efficacy Thesaurus, Application Domain, Technology Topic, Popular Technical Reports.
© 2025 PatSnap. All rights reserved.Legal|Privacy policy|Modern Slavery Act Transparency Statement|Sitemap|About US| Contact US: help@patsnap.com