High speed wire package type neatening equipment and control method thereof
A control method and regular technology, applied in the field of steel rolling, can solve the problem of easy occurrence of floating wire and other problems
- Summary
- Abstract
- Description
- Claims
- Application Information
AI Technical Summary
Problems solved by technology
Method used
Image
Examples
Embodiment 1
[0035] Embodiment 1: A control method for high wire package shape regulation, which is used for Φ5.5mm welding wire steel, comprising the following steps:
[0036] S1, adjust the angle of the left supporting plate 34, its adjustment range is 20 ° ~ 30 °, adjust the height of the lower supporting plate 35, its adjustment range is 10 ° ~ 20 °, adjust the height of the right supporting plate 36, its adjustment range is 20°~30°, raise the height of the first cooling roller table 4 adjacent to the laying head 3, and the lifting range is 60mm~80mm;
[0037] S2. Adjust the distance between the first vertical roller 8 and the second vertical roller 10, between 1080mm and 1090mm;
[0038] S3. Adjust the gap between the deflector plate 31 and the split plate 37, between 2.5mm and 3.5mm;
[0039] S4, adjust the speed of the laying head 3 so that the speed of the laying head 3 is 0.5m / s smaller than the speed of the finishing mill 1;
[0040] S5. Adjust the spinning machine 3 so that th...
Embodiment 2
[0043] Embodiment 2: A control method for high wire wrap shape regulation, which is used for Φ6.5mm cold heading steel, including the following steps:
[0044] S1, adjust the angle of the left supporting plate 34, its adjustment range is 15 ° ~ 25 °, adjust the height of the lower supporting plate 35, its adjustment range is 5 ° ~ 15 °, adjust the height of the right supporting plate 36, its adjustment range is 15°~25°, the height of the first cooling roller table 4 adjacent to the laying head 3 is raised, and the lifting range is 70mm~90mm;
[0045] S2. Adjust the distance between the first vertical roller 8 and the second vertical roller 10, between 1085mm and 1095mm;
[0046] S3. Adjust the gap between the deflector plate 31 and the split plate 37, between 2.5 mm and 4 mm;
[0047] S4, adjust the speed of the laying head 3 so that the speed of the laying head 3 is 0.5m / s smaller than the speed of the finishing mill 1;
[0048] S5. Adjust the spinning machine 3 so that the...
PUM
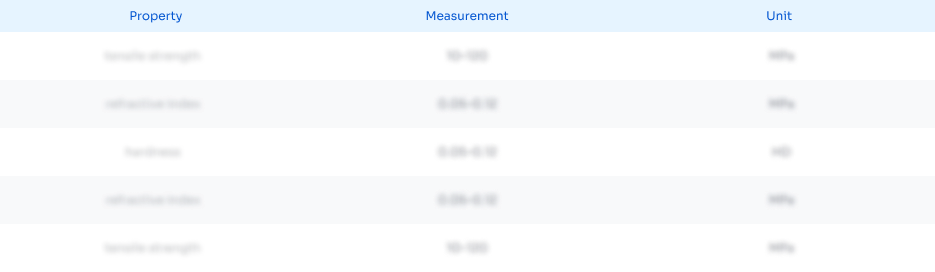
Abstract
Description
Claims
Application Information

- Generate Ideas
- Intellectual Property
- Life Sciences
- Materials
- Tech Scout
- Unparalleled Data Quality
- Higher Quality Content
- 60% Fewer Hallucinations
Browse by: Latest US Patents, China's latest patents, Technical Efficacy Thesaurus, Application Domain, Technology Topic, Popular Technical Reports.
© 2025 PatSnap. All rights reserved.Legal|Privacy policy|Modern Slavery Act Transparency Statement|Sitemap|About US| Contact US: help@patsnap.com