Efficient multi-stage braking mechanism
A braking mechanism, efficient technology
- Summary
- Abstract
- Description
- Claims
- Application Information
AI Technical Summary
Problems solved by technology
Method used
Image
Examples
Embodiment 1
[0052] figure 1 It is a structural schematic diagram of Embodiment 1 of this mechanism. Such as figure 1 It can be seen that the mechanism includes a housing 2 , a plunger sleeve 4 arranged on the housing 2 and reciprocating relative to the housing 2 , a plunger 5 arranged on the plunger sleeve 4 and reciprocating relative to the plunger sleeve 4 , and a hydraulic control unit 12 . A second oil chamber Q2 is formed between the plunger 5 and the plunger sleeve 4 . A collar is provided on the plunger sleeve 4 as a limit setting for limiting the maximum volume of the second oil chamber Q2. Two first passages 7 are arranged on the side wall of the plunger sleeve 4 , and each first passage 7 is provided with a locking body 6 that reciprocates relative to the first passage 7 . A first oil chamber Q1 is formed between the plunger sleeve 4 , the housing 2 and the locking body 6 . The hydraulic control unit 12 is connected to the first oil chamber Q1 through the first oil passage...
Embodiment 2
[0059] image 3 It is a structural schematic diagram of Embodiment 2 of this mechanism. Such as image 3 It can be seen that the mechanism includes a housing 2 , a plunger sleeve 4 fixed on the housing 2 , a plunger 5 arranged on the plunger sleeve 4 and reciprocating relative to the plunger sleeve 4 , and a hydraulic control unit 12 . A second oil chamber Q2 is formed between the plunger 5 and the plunger sleeve 4 . A shoulder is set on the plunger sleeve 4 to limit the limit setting of the maximum volume of the second oil chamber Q2. Three first passages 7 uniformly distributed in the circumferential direction are arranged on the side wall of the plunger sleeve 4 , and each first passage 7 is respectively provided with a locking body 6 that reciprocates relative to the first passage 7 .
[0060] image 3 The third reset scheme is adopted, the side wall of the plunger 5 is provided with a circumferential groove, the third oil chamber Q3 is arranged between the plunger 5, ...
PUM
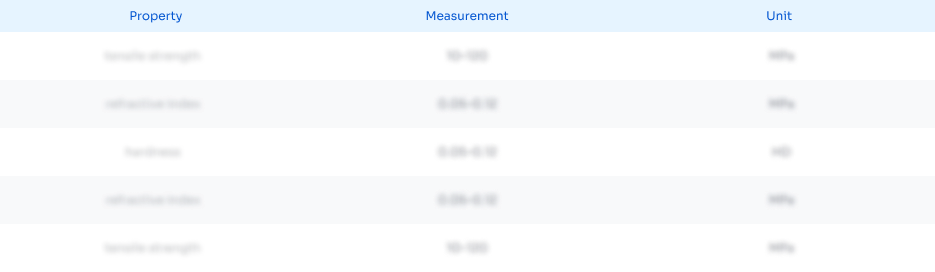
Abstract
Description
Claims
Application Information

- R&D Engineer
- R&D Manager
- IP Professional
- Industry Leading Data Capabilities
- Powerful AI technology
- Patent DNA Extraction
Browse by: Latest US Patents, China's latest patents, Technical Efficacy Thesaurus, Application Domain, Technology Topic, Popular Technical Reports.
© 2024 PatSnap. All rights reserved.Legal|Privacy policy|Modern Slavery Act Transparency Statement|Sitemap|About US| Contact US: help@patsnap.com