3D texture electroforming reprinting injection molding part, mold and process
A technology of injection molding and texture, applied in electrical components, household appliances, telephone communication, etc., can solve the problems of low production cost, laser burning residue, high production efficiency, reduce production cost, improve processing efficiency, and facilitate mold drafting Effect
- Summary
- Abstract
- Description
- Claims
- Application Information
AI Technical Summary
Problems solved by technology
Method used
Image
Examples
Embodiment Construction
[0029] The present invention will be described in detail below in conjunction with the accompanying drawings.
[0030] Such as figure 1 , figure 2 As shown, the 3D texture electroforming reprinting injection molded part of the present invention includes a main body 1 and an outer edge 2, the outer edge 2 is located on the outer edge of the main body 1, the cross section of the outer edge 2 is in a inferior arc shape, and the outer edge 2 The edge portion 2 is connected tangentially to the main body portion 1, and the length of the chord formed by the point at the junction of the outer edge portion 2 and the main body portion 1 and the point at the end of the cross section of the outer edge portion 2 is smaller than the radius of curvature of the outer edge portion 2; The surface of the main body 1 and the outer edge 2 has a plurality of optical texture grooves arranged in an array; the depth of the optical texture groove is greater than 0.003mm and less than 0.006mm, and the...
PUM
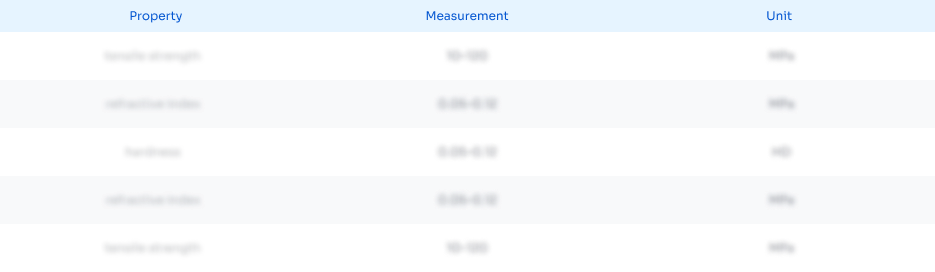
Abstract
Description
Claims
Application Information

- R&D
- Intellectual Property
- Life Sciences
- Materials
- Tech Scout
- Unparalleled Data Quality
- Higher Quality Content
- 60% Fewer Hallucinations
Browse by: Latest US Patents, China's latest patents, Technical Efficacy Thesaurus, Application Domain, Technology Topic, Popular Technical Reports.
© 2025 PatSnap. All rights reserved.Legal|Privacy policy|Modern Slavery Act Transparency Statement|Sitemap|About US| Contact US: help@patsnap.com