Automatic machining equipment for double-head terminal crimping sleeve
An automatic processing and casing technology, which is applied to equipment for connecting/terminating cables, equipment for dismantling/armoring cables, and cable installation devices, etc. It can solve the problems of low automation, high cost of industrial robots, and inability to obtain accuracy Security and other issues
- Summary
- Abstract
- Description
- Claims
- Application Information
AI Technical Summary
Problems solved by technology
Method used
Image
Examples
Embodiment Construction
[0045] The present invention will be described in detail below in conjunction with the accompanying drawings.
[0046] Such as Figure 1-3 As shown, the automatic processing equipment for double-ended end casings includes a workbench 0, a first processing tool 1 is provided at one end of the workbench 0, and the first processing tool 1 includes a wire feeding device 2 and a wire stripping device 3 and casing device 4;
[0047] More specifically, see Figure 6 , the wire feeding device 2 includes a slide table 21, the slide table 21 is provided with a wire feed transmission device 22 and a wire feed drive device 23 providing power for the slide table 21, and the top of the slide table 21 is provided with four crimping wheels 24 and the wire feeding power device 25 that drives the crimping wheel 24 to work. The finger cylinder 26 is installed on the top of the crimping wheel 24. The clamping place of the finger cylinder 26 corresponds to the outlet of the crimping wheel 24. Th...
PUM
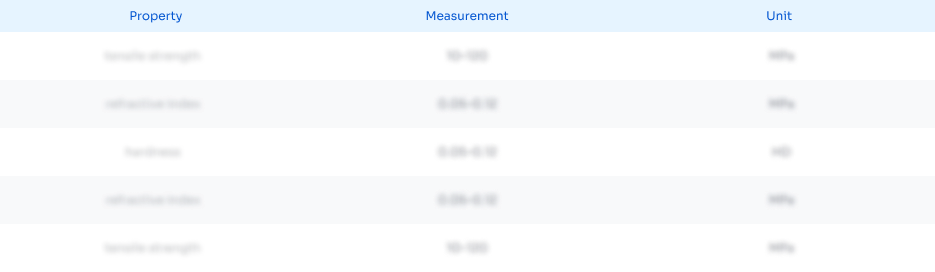
Abstract
Description
Claims
Application Information

- Generate Ideas
- Intellectual Property
- Life Sciences
- Materials
- Tech Scout
- Unparalleled Data Quality
- Higher Quality Content
- 60% Fewer Hallucinations
Browse by: Latest US Patents, China's latest patents, Technical Efficacy Thesaurus, Application Domain, Technology Topic, Popular Technical Reports.
© 2025 PatSnap. All rights reserved.Legal|Privacy policy|Modern Slavery Act Transparency Statement|Sitemap|About US| Contact US: help@patsnap.com