Method for preparing polyformaldehyde through co-production of trioxymethylene and dioxolane
A technology of paraformaldehyde and dioxane, applied in the direction of sustainable manufacturing/processing, organic chemistry, climate sustainability, etc., can solve the problems of corrosive equipment and pipelines, rectification column equipment pipeline blockage, large pollution, etc.
- Summary
- Abstract
- Description
- Claims
- Application Information
AI Technical Summary
Problems solved by technology
Method used
Image
Examples
Embodiment 1
[0071] A method for preparing polyoxymethylene by co-production of paraformaldehyde and dioxane, comprising the following steps:
[0072] Step 1: the 37% formaldehyde solution produced by the Ag method is concentrated to obtain 58% formaldehyde solution stream 1 and the paraformaldehyde enrichment tower (T1101) tower kettle recycle stream 3 mixes and enters the paraformaldehyde that molecular sieve catalyst is housed in advance In the reactor (R1101), the molecular sieve catalyst filling mass is 5% of the reaction solution, the reaction temperature is 100°C, and the reaction pressure is -0.05MPa. The aqueous solution stream 2 of paraformaldehyde and formaldehyde is recovered in the gas phase at the outlet of the reactor, and its composition is: 39% of formaldehyde, 20% of paraformaldehyde and 41% of water.
[0073] Stream 2 is fed from the 8th tray in the middle of the tower, and enters the paraformaldehyde concentration tower (T1101), the number of trays is 20, the temperatur...
Embodiment 2
[0080] A method for preparing polyoxymethylene by co-production of paraformaldehyde and dioxane, comprising the following steps:
[0081] Step 1: enter the paraformaldehyde reactor (R1101) that the resin catalyst is pre-installed after the 60% formaldehyde aqueous solution stream 1 that iron molybdenum is produced is mixed with the paraformaldehyde enrichment tower (T1101) tower bottom recycle stream 3, and the resin catalyst The filling mass is 15% of the reaction solution, the reaction temperature is 102° C., and the reaction pressure is normal pressure. The aqueous solution stream 2 of paraformaldehyde and formaldehyde is recovered in the gas phase at the outlet of the reactor, and its composition is: 41% of formaldehyde, 16% of paraformaldehyde and 43% of water.
[0082] Stream 2 is fed from the 10th tray in the middle of the tower, and enters the paraformaldehyde concentration tower (T1101), the number of trays is 22, the temperature of the tower bottom is 73°C, the tempe...
Embodiment 3
[0090] A device for preparing polyoxymethylene by co-producing paraformaldehyde and dioxane, comprising three units: a paraformaldehyde monomer preparation unit, a dioxane monomer preparation unit and a polyoxymethylene preparation unit.
[0091] The paraformaldehyde monomer preparation unit comprises a paraformaldehyde reactor (R1101), a paraformaldehyde concentration tower (T1101), a paraformaldehyde dealdehyde tower (T1102) and a paraformaldehyde membrane dehydration device (M1101); The dioxane monomer preparation unit includes a low water content hemiacetal membrane dehydration device (M2201), a dioxane reactive distillation tower (R1201) and a dioxane membrane dehydration device (M1202); the polyoxymethylene preparation unit Consists of polyoxymethylene reactor (R2301).
[0092] (1) Paraformaldehyde monomer preparation unit
[0093] The 60% formaldehyde aqueous solution stream 1 that iron molybdenum produces enters the paraformaldehyde reactor (R1101) that the resin cata...
PUM
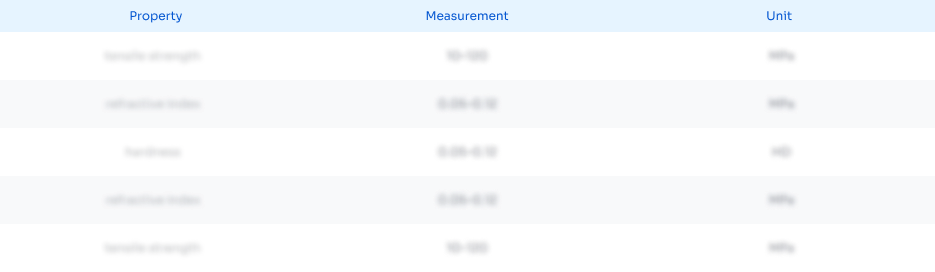
Abstract
Description
Claims
Application Information

- R&D Engineer
- R&D Manager
- IP Professional
- Industry Leading Data Capabilities
- Powerful AI technology
- Patent DNA Extraction
Browse by: Latest US Patents, China's latest patents, Technical Efficacy Thesaurus, Application Domain, Technology Topic, Popular Technical Reports.
© 2024 PatSnap. All rights reserved.Legal|Privacy policy|Modern Slavery Act Transparency Statement|Sitemap|About US| Contact US: help@patsnap.com