A method of electrochemistry-impregnation collaborative preparation of graphite resistance to high temperature composite coating
A composite coating and high-temperature-resistant technology, which is applied in the field of graphite high-temperature coating, can solve the problems of inability to meet the oxidation resistance requirements of graphite materials, poor bonding between the coating and the substrate, and insufficient air tightness of the coating, so as to facilitate industrial production and application , not easy to fall off, good air tightness effect
- Summary
- Abstract
- Description
- Claims
- Application Information
AI Technical Summary
Problems solved by technology
Method used
Image
Examples
Embodiment 1
[0027] (1) Graphite base material is selected, the surface is polished and ultrasonically treated with anhydrous ethanol. After the surface is dried, it is placed in an oven and placed at 100 ° C for 2 hours until use.
[0028] (2) Preparation of matrix suspension: silicon carbide 18g / L, alumina 5g / L, aluminum phosphate 8g / L, phenolic resin 10g / L, nano silicon powder 6g / L, graphite powder 3g / L, dodecyl Sodium benzenesulfonate 2g / L and the rest were added to 1L with ethanol, followed by ultrasonic treatment for 60min to obtain a matrix suspension.
[0029] (3) Preparation of phosphate coating: weigh 35g of aluminum dihydrogen phosphate, 7g of sodium hexametaphosphate, 2g of nano-alumina, 3g of silicon dioxide, 1g of sodium dodecylbenzenesulfonate, and 52g of solvent water, and then carry out 60min of Ball milling to obtain phosphate coating;
[0030] (4) Fix it with an electrochemical clamp, adjust and place it in parallel between two high-purity graphite blocks, connect the w...
Embodiment 2
[0036] (1) Graphite base material is selected, the surface is polished and ultrasonically treated with anhydrous ethanol. After the surface is dried, it is placed in an oven and placed at 100 ° C for 2 hours until use.
[0037] (2) Preparation of matrix suspension: 10g / L of silicon carbide, 5g / L of alumina, 9g / L of aluminum phosphate, 12g / L of phenolic resin, 10g / L of nano-silicon powder, 4g / L of graphite powder, dodecyl Sodium benzenesulfonate 2g / L and the rest were added to 1L with ethanol, followed by ultrasonic treatment for 60min to obtain a matrix suspension.
[0038] (3) Preparation of phosphate coating: weigh 25g of aluminum dihydrogen phosphate, 10g of magnesium dihydrogen phosphate, 7g of sodium hexametaphosphate, 1.5g of nano-alumina, 3.5g of silicon dioxide, 1g of sodium dodecylbenzenesulfonate, Solvent water 52g, then carry out the ball milling treatment of 60min, obtain phosphate dipping solution;
[0039] (4) Fix it with an electrochemical clamp, adjust and pla...
Embodiment 3
[0045] (1) Graphite base material is selected, the surface is polished and ultrasonically treated with anhydrous ethanol. After the surface is dried, it is placed in an oven and placed at 100 ° C for 2 hours until use.
[0046] (2) Preparation of matrix suspension: 10g / L of silicon carbide, 5g / L of alumina, 9g / L of aluminum phosphate, 12g / L of phenolic resin, 10g / L of nano-silicon powder, 4g / L of graphite powder, dodecyl Sodium benzenesulfonate 2g / L and the rest were added to 1L with ethanol, followed by ultrasonic treatment for 60min to obtain a matrix suspension.
[0047] (4) Fix it with an electrochemical clamp, adjust and place it in parallel between two high-purity graphite blocks, connect the working electrode, and use the calomel electrode as the reference electrode, select CHI606 electrochemical workstation, i-t curve, set voltage 10V, time 250S, electrochemical deposition in substrate suspension.
[0048] (5) After the graphite substrate is coated by electrochemical ...
PUM
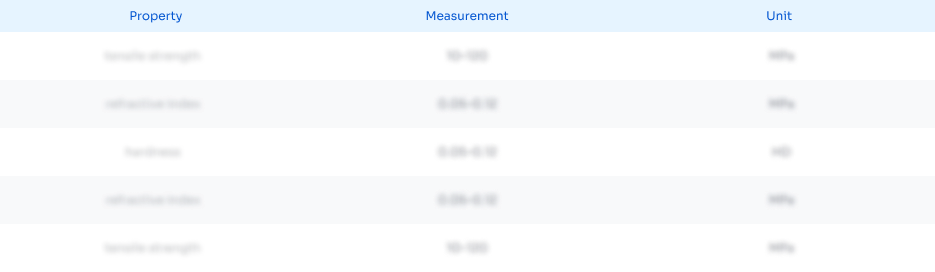
Abstract
Description
Claims
Application Information

- Generate Ideas
- Intellectual Property
- Life Sciences
- Materials
- Tech Scout
- Unparalleled Data Quality
- Higher Quality Content
- 60% Fewer Hallucinations
Browse by: Latest US Patents, China's latest patents, Technical Efficacy Thesaurus, Application Domain, Technology Topic, Popular Technical Reports.
© 2025 PatSnap. All rights reserved.Legal|Privacy policy|Modern Slavery Act Transparency Statement|Sitemap|About US| Contact US: help@patsnap.com