Medium-frequency induction heating furnace body, furnace body manufacturing method and temperature control method
An induction heating furnace and manufacturing method technology, applied in the furnace body manufacturing method and temperature control, in the field of medium-frequency induction heating furnace body, can solve the problems of scale formation, low temperature signal of the thermometer, and contact with air, etc., to achieve Simplify the manufacturing process, ensure the pass rate, and ensure the effect of not overheating
- Summary
- Abstract
- Description
- Claims
- Application Information
AI Technical Summary
Problems solved by technology
Method used
Image
Examples
Embodiment 1
[0048] refer to figure 2 As shown, this embodiment provides a medium frequency induction heating furnace body, including a furnace shell 4 and a furnace lining 1, and a forehearth 11 is provided in the middle of the furnace lining 1 for the blank to pass through. During forging, the blank passes along the forehearth 11 Axial travel.
[0049] The furnace lining 1 is provided with an induction coil 2 that extends axially along the forehearth 11 and is spirally wound outside the forehearth 11 ; wherein the induction coil 2 is wound by a copper tube.
[0050] The side wall of the furnace lining 1 is spaced apart from a number of temperature measuring holes 12 distributed along the axial direction of the furnace lining 1, wherein the temperature measuring holes 12 are arranged radially along the furnace lining 1 and communicate with the material channel 11 through the side wall of the furnace lining 1. The temperature hole 12 is located at the interval between two adjacent turns ...
Embodiment 2
[0062] Such as Figure 2-Figure 4 As shown, the present embodiment provides a method for manufacturing the intermediate frequency induction heating furnace described in Embodiment 1, which specifically includes the following steps:
[0063] S100. Winding the induction coil 2: place the copper tube on the copper tube winding machine, wind the copper tube in a spiral shape through the copper tube winding machine to form a section of induction coil 2; repeat this step, and wind several sections according to actual needs Induction coil 2.
[0064] Finally, all the induction coils 2 are connected and formed in series or in parallel, and it should be noted that the induction coils 2 are arranged coaxially.
[0065] In this step, according to the position of the temperature measuring hole 12 that needs to be opened, the gap between the two turns of the induction coil 2 corresponding to the positions on both sides of the temperature measuring hole 12 is appropriately increased, so as...
Embodiment 3
[0086] combine figure 1 As shown, this embodiment provides a temperature control method applied to the electric furnace body 01 in Embodiment 1, which specifically includes the following steps:
[0087] In the first step, the temperature measuring instrument 9 coaxially arranged with the temperature measuring hole 12 is correspondingly installed outside each of the temperature measuring holes 12 (the temperature measuring instrument at the temperature measuring hole is not shown), wherein the temperature measuring instrument 9 is specifically Infrared thermometers can be used.
[0088] All the thermometers 9 are connected with the control device, and the control device is used to control and adjust the input power of the induction coil 2 according to the temperature signal fed back by the thermometer 9 . The control device can be a PLC or a finished instrument, and of course it can also be other control devices, which are not specifically limited here; the following uses PLC ...
PUM
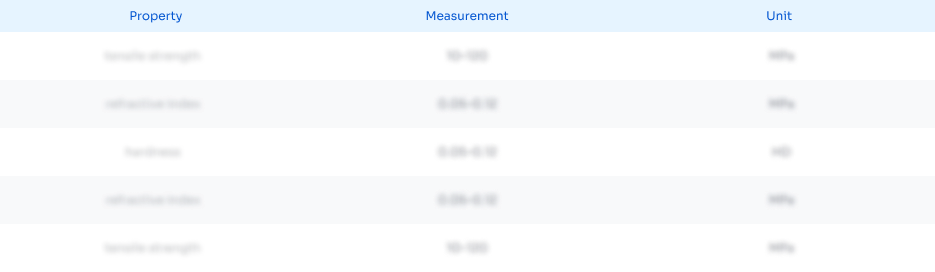
Abstract
Description
Claims
Application Information

- Generate Ideas
- Intellectual Property
- Life Sciences
- Materials
- Tech Scout
- Unparalleled Data Quality
- Higher Quality Content
- 60% Fewer Hallucinations
Browse by: Latest US Patents, China's latest patents, Technical Efficacy Thesaurus, Application Domain, Technology Topic, Popular Technical Reports.
© 2025 PatSnap. All rights reserved.Legal|Privacy policy|Modern Slavery Act Transparency Statement|Sitemap|About US| Contact US: help@patsnap.com