A device and method for depositing pure DLC by graphite cathode arc enhanced glow discharge
A technology of graphite cathode and glow discharge, applied in vacuum evaporation plating, coating, gaseous chemical plating, etc., can solve problems such as metal element pollution, achieve quality assurance, easy film composition and performance, and low cost Effect
- Summary
- Abstract
- Description
- Claims
- Application Information
AI Technical Summary
Problems solved by technology
Method used
Image
Examples
specific Embodiment approach 1
[0029]Embodiment 1: In this embodiment, a graphite cathode arc-enhanced glow discharge deposition pure DLC device includes a vacuum chamber 9, a turret 2, a bias power supply 10, a first graphite cathode arc 1-1, and a second graphite cathode arc 1-2. First metal cathode 5-1, second metal cathode 5-2, first anode 3-1, second anode 3-2, first high pulse power supply 4-1, second high pulse power supply 4- 2. The first DC power supply 6-1 and the second DC power supply 6-2; the bottom of the vacuum chamber 9 is provided with an air inlet 7; , four flanges are evenly arranged on the wall of the vacuum chamber 9 along the circumferential direction, and the four flanges are respectively fixedly connected to the first graphite cathode arc 1-1, the first metal cathode 5-1, and the second graphite cathode arc 1-2 And the second metal cathode 5-2; the first graphite cathode arc 1-1 and the second graphite cathode arc 1-2 and the turret 2 are provided with a baffle 8, and the two ends of...
specific Embodiment approach 2
[0031] Embodiment 2: The difference between this embodiment and Embodiment 1 is that the turret 2, the first graphite cathode arc 1-1, the second graphite cathode arc 1-2, the first metal cathode 5-1, and the second metal cathode The cathode 5 - 2 , the first anode 3 - 1 , the second anode 3 - 2 , and the baffle 8 are all insulated from the vacuum chamber 9 . Others are the same as the first embodiment.
[0032] In this embodiment, the turret 2, the first graphite cathode arc 1-1, the second graphite cathode arc 1-2, the first metal cathode 5-1, the second metal cathode 5-2, the first anode 3-1, the second The anode 3-2 and the baffle 8 are insulated from the vacuum chamber 9 by polytetrafluoroethylene.
specific Embodiment approach 3
[0033] Embodiment 3: The difference between this embodiment and Embodiment 1 or 2 is that the electrical connection terminal of the first anode 3-1 is electrically connected to the positive electrode of the first high-pulse power supply 4-1, and the first high-pulse power supply 4- The negative pole of 1 is electrically connected to the electrical connection terminal of the first graphite cathode arc 1-1; the electrical connection terminal of the second anode 3-2 is electrically connected to the positive pole of the second high-pulse power supply 4-2, and the second high-pulse power supply 4- The negative electrode of 2 is electrically connected to the electrical connection end of the second graphite cathode arc 1-2. Others are the same as in the first or second embodiment.
PUM
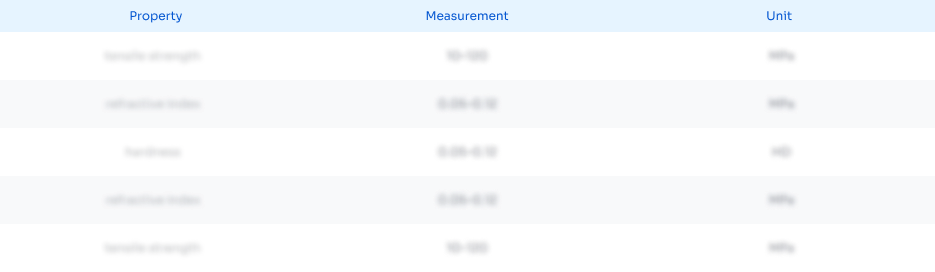
Abstract
Description
Claims
Application Information

- R&D
- Intellectual Property
- Life Sciences
- Materials
- Tech Scout
- Unparalleled Data Quality
- Higher Quality Content
- 60% Fewer Hallucinations
Browse by: Latest US Patents, China's latest patents, Technical Efficacy Thesaurus, Application Domain, Technology Topic, Popular Technical Reports.
© 2025 PatSnap. All rights reserved.Legal|Privacy policy|Modern Slavery Act Transparency Statement|Sitemap|About US| Contact US: help@patsnap.com