Ultrahigh-conductivity nano carbon masterbatch as well as preparation method and application thereof
A conductive nanometer and masterbatch technology, applied in the field of ultra-high conductive nanocarbon masterbatch and its preparation, can solve the problems of difficulty, loss of graphene, difficult processing and compatibility, and achieve uniform distribution, reduce agglomeration, and improve compatibility. Effect
- Summary
- Abstract
- Description
- Claims
- Application Information
AI Technical Summary
Problems solved by technology
Method used
Image
Examples
Embodiment 1
[0034] (1) First put multi-walled carbon nanotubes: porous graphene: coupling agent into a high-mixer at a mass ratio of 1:2:0.5, and mix at a temperature of 80-90°C for 3 minutes to prepare conductive nanocarbons ;
[0035] (2) Then add 30 parts of polycarbonate, 67 parts of conductive nano-carbon, 1 part of main antioxidant, 1 part of auxiliary antioxidant, and 1 part of high-efficiency dispersant into the internal mixer for banburying, and the banburying temperature is 270°C , the rotor speed is 40r / min, and the mixing time is 30min;
[0036] (3) Then import it into a single-screw extruder for granulation to obtain an ultra-high conductive nano-carbon masterbatch material.
Embodiment 2
[0038] (1) First put multi-walled carbon nanotubes: porous graphene: coupling agent into a high-mixer at a mass ratio of 1:3:1, and mix at a temperature of 80-90°C for 5 minutes to prepare conductive nanocarbons ;
[0039] (2) Then add 47.5 parts of polycarbonate, 50 parts of conductive nano-carbon, 0.7 part of primary antioxidant, 0.8 part of auxiliary antioxidant, and 1 part of high-efficiency dispersant into the internal mixer for banburying, and the banburying temperature is 280 ° C , rotor speed 55r / min, banburying time 45min;
[0040] (3) Then import it into a single-screw extruder for granulation to obtain an ultra-high conductive nano-carbon masterbatch material.
Embodiment 3
[0042] (1) First put multi-walled carbon nanotubes: porous graphene: coupling agent into a high-mixer at a mass ratio of 1:4:2, and mix at 80-90°C for 5 minutes to prepare conductive nanocarbons ;
[0043] (2) Add 58.5 parts of polycarbonate, 40 parts of conductive nano-carbon, 0.5 part of primary antioxidant, 0.5 part of auxiliary antioxidant, and 0.5 part of high-efficiency dispersant into the internal mixer for banburying, and the banburying temperature is 280°C , rotor speed 55r / min, banburying time 45min;
[0044] (3) Then import it into a single-screw extruder for granulation to obtain an ultra-high conductive nano-carbon masterbatch material.
PUM
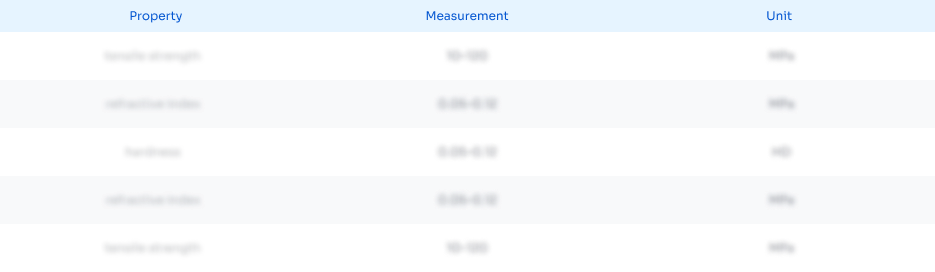
Abstract
Description
Claims
Application Information

- R&D
- Intellectual Property
- Life Sciences
- Materials
- Tech Scout
- Unparalleled Data Quality
- Higher Quality Content
- 60% Fewer Hallucinations
Browse by: Latest US Patents, China's latest patents, Technical Efficacy Thesaurus, Application Domain, Technology Topic, Popular Technical Reports.
© 2025 PatSnap. All rights reserved.Legal|Privacy policy|Modern Slavery Act Transparency Statement|Sitemap|About US| Contact US: help@patsnap.com