Carbon fiber reinforced SiAlOC composite material and preparation method thereof
A composite material and carbon fiber technology, which is applied in the field of carbon fiber reinforced SiAlOC composite material and its preparation, can solve the problems of poor mechanical properties of composite materials, low densification efficiency, and low ceramic yield, and achieve good mechanical properties and high temperature resistance. Improve mechanical properties and facilitate operation
- Summary
- Abstract
- Description
- Claims
- Application Information
AI Technical Summary
Problems solved by technology
Method used
Image
Examples
Embodiment 1
[0026] A preparation method of carbon fiber reinforced SiAlOC composite material, comprising the following steps:
[0027] (1) Impregnation: Prepare the three-dimensional four-way braid and place it under vacuum conditions with a pressure of less than 500Pa, and use Al(NO 3 ) 3 9H 2 O and silicone resin mass ratio of 1:5 containing Al-containing polysiloxane precursor solution immersion 1h;
[0028] The polysiloxane precursor solution containing Al is a mixed sol of aluminum-containing sol and silicone resin ethanol solution, and the aluminum-containing sol is composed of Al(NO 3 ) 3 9H 2 O is dissolved in ethanol to obtain, Al(NO 3 ) 3 9H 2 The mass ratio of O to ethanol is 3:10, the mass concentration of the silicone resin ethanol solution is 20%, and the silicone resin is selected from small molecular weight methyl silicone resin (MK);
[0029] (2) Curing: heat the impregnated carbon fiber preform at 60°C for 48 hours until it gels, and then cross-link and cure the ...
Embodiment 2
[0036] A preparation method of carbon fiber reinforced SiAlOC composite material, comprising the following steps:
[0037] (1) Impregnation: Prepare the plain weave laminated stitched preform and place it under a vacuum condition with a pressure less than 500Pa, and use Al(NO 3 ) 3 9H 2 Immerse in an Al-containing polysiloxane precursor solution with a mass ratio of O to silicone resin of 3:10 for 1 h;
[0038] The polysiloxane precursor solution containing Al is a mixed sol of aluminum-containing sol and silicone resin ethanol solution, and the aluminum-containing sol is composed of Al(NO 3 ) 3 9H 2 O is dissolved in ethanol to obtain, Al(NO 3 ) 3 9H 2 The mass ratio of O to ethanol is 1:5, the mass concentration of the silicone resin ethanol solution is 60%, and the silicone resin is selected from small molecular weight methyl silicone resin (MK);
[0039](2) Curing: heat the impregnated carbon fiber preform at 70°C for 30h until it gels, and then cross-link and cure...
Embodiment 3
[0045] A preparation method of carbon fiber reinforced SiAlOC composite material, comprising the following steps:
[0046] (1) Impregnation: Prepare a 2.5-dimensional braid and place it under vacuum conditions with a pressure of less than 500Pa, and use Al(NO 3 ) 3 9H 2 The Al-containing polysiloxane precursor solution with a mass ratio of O to silicone resin of 2.5:10 was immersed for 3 hours;
[0047] The polysiloxane precursor solution containing Al is a mixed sol of aluminum-containing sol and silicone resin ethanol solution, and the aluminum-containing sol is composed of Al(NO 3 ) 3 9H 2 O is dissolved in ethanol to obtain, Al(NO 3 ) 3 9H 2 The mass ratio of O to ethanol is 1:2, the mass concentration of the silicone resin ethanol solution is 40%, and the silicone resin is selected from small molecular weight methyl silicone resin (MK);
[0048] (2) Curing: heat the impregnated carbon fiber preform at 80°C for 24 hours until it gels, and then cross-link and cure t...
PUM
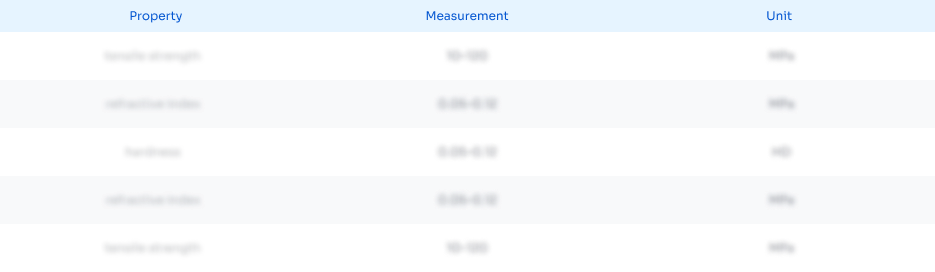
Abstract
Description
Claims
Application Information

- R&D
- Intellectual Property
- Life Sciences
- Materials
- Tech Scout
- Unparalleled Data Quality
- Higher Quality Content
- 60% Fewer Hallucinations
Browse by: Latest US Patents, China's latest patents, Technical Efficacy Thesaurus, Application Domain, Technology Topic, Popular Technical Reports.
© 2025 PatSnap. All rights reserved.Legal|Privacy policy|Modern Slavery Act Transparency Statement|Sitemap|About US| Contact US: help@patsnap.com