Novel assembly type connecting joint
A connection node and prefabricated technology, applied in the direction of buildings and building structures, can solve the problems of connection stiffness not meeting the requirements, too many components at the nodes, unstable quality, etc. The effect of reducing the number of components
- Summary
- Abstract
- Description
- Claims
- Application Information
AI Technical Summary
Problems solved by technology
Method used
Image
Examples
Embodiment 1
[0034] A new type of prefabricated connection node, comprising a prefabricated corbel column 1 and a prefabricated beam 2, at least one set of corbels 3 of the prefabricated corbel column 1 is provided, and two of the corbels 3 in one set are symmetrical to the prefabricated The corbel 1 and the corbel 3 are usually arranged at the waist of the prefabricated corbel 1,
[0035] Screw A4, the screw A4 is fixed on the corbel and parallel to the prefabricated corbel column 1, and the end of the prefabricated beam 2 rests on the corbel 3 and is connected by bolt fit;
[0036] The first through hole 5, the first through hole 5 runs through the end of the prefabricated beam 2 and corresponds to the screw A4; the screw A4 passes through the first through hole 5 and extends to the first through hole 5 Out of a through hole 5;
[0037] Groove, the groove is set on the end surface of the prefabricated beam 2, including the first groove 7 set on the upper end of the first through hole 5 ...
Embodiment 2
[0041] According to the prefabricated height or construction requirements, different corbels can be connected to achieve the required length. On the basis of the above-mentioned embodiment 1, this embodiment 2 only makes improvements in the joint connection mode of the prefabricated corbel column 1, and the joint connection mode between the prefabricated corbel column 1 and the prefabricated beam 2 is the same as above, I won't go into details.
[0042] There may be multiple prefabricated corbels 1, and the prefabricated corbels 1 are connected by a mortise and tenon structure.
[0043]The mortise and tenon structure includes a mortise 10 at one end of the prefabricated corbel 1 and a mortise 11 at the other end of the prefabricated corbel 1. The mortise 10 is cross-shaped, and the mortise 11 is in line with the The tenon 10 matches the cross groove, and the tenon 10 and the mortise 11 are fixed by means of bolt connection.
[0044] A square notch 12 is reserved at the four ...
PUM
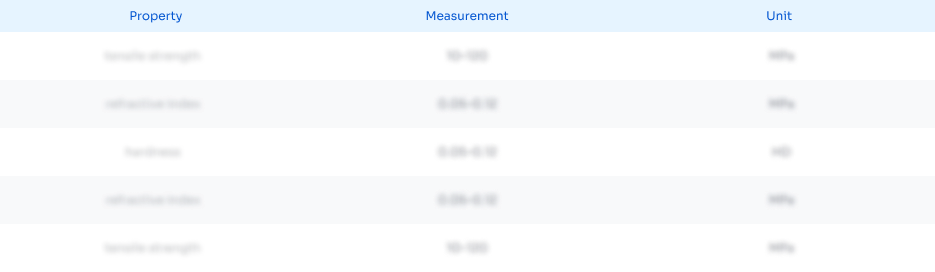
Abstract
Description
Claims
Application Information

- R&D Engineer
- R&D Manager
- IP Professional
- Industry Leading Data Capabilities
- Powerful AI technology
- Patent DNA Extraction
Browse by: Latest US Patents, China's latest patents, Technical Efficacy Thesaurus, Application Domain, Technology Topic, Popular Technical Reports.
© 2024 PatSnap. All rights reserved.Legal|Privacy policy|Modern Slavery Act Transparency Statement|Sitemap|About US| Contact US: help@patsnap.com