Supercritical carbon dioxide waterless dyeing system and method
A carbon dioxide and water-free dyeing technology, which is applied in the field of dyeing equipment and dyeing technology, can solve the problems of affecting the yield, oligomer pollution, stains, etc., and achieve the effect of improving production capacity and reducing equipment investment
- Summary
- Abstract
- Description
- Claims
- Application Information
AI Technical Summary
Problems solved by technology
Method used
Image
Examples
Embodiment 1
[0056] The specific process of dyeing polyester filament cheese is as follows:
[0057] (1) CO 2 Tank storage for liquid CO 2 , the liquid CO is pumped through the delivery pump 2 delivered to CO 2 Circulation storage tank (liquid level reaches CO 2 Turn off the delivery pump when circulating 2 / 3 of the storage tank and stop the delivery).
[0058] (2) Turn on the low-temperature booster pump and turn on the CO 2 Circulating liquid CO in storage tanks 2 Pump into the staining system.
[0059] (3) Turn on the heating and turn on the circulation pump at the same time. After the temperature rises to the temperature required for the deoiling process, use the extraction function of supercritical carbon dioxide to remove the oil on the dyed polyester filament cheese. Turn on the separation and recovery unit to separate the oil agent from carbon dioxide and recover clean carbon dioxide. At the same time, turn on the low-temperature booster pump to pump new carbon dioxide into ...
Embodiment 2
[0064] The specific process of dyeing polyester gray cloth is as follows:
[0065] (1) CO 2 Tank storage for liquid CO 2 , the liquid CO is pumped through the delivery pump 2 delivered to CO 2 Circulation storage tank (liquid level reaches CO 2 Turn off the delivery pump when circulating 2 / 3 of the storage tank and stop the delivery).
[0066] (2) Turn on the low-temperature booster pump and turn on the CO 2 Circulating liquid CO in storage tanks 2 Pump into the staining system.
[0067](3) Turn on the heating and turn on the circulation pump at the same time. After the temperature rises to the temperature required for the deoiling process, use the extraction function of supercritical carbon dioxide to remove the oil on the polyester gray cloth. Turn on the separation and recovery unit to separate the oil agent from carbon dioxide and recover clean carbon dioxide. At the same time, turn on the low-temperature booster pump to pump new carbon dioxide into the system.
[...
Embodiment 3
[0072] The specific process of dyeing polyester loose fiber is as follows:
[0073] (1) CO 2 Tank storage for liquid CO 2 , the liquid CO is pumped through the delivery pump 2 delivered to CO 2 Circulation storage tank (liquid level reaches CO 2 Turn off the delivery pump when circulating 2 / 3 of the storage tank and stop the delivery).
[0074] (2) Turn on the low-temperature booster pump and turn on the CO 2 Circulating liquid CO in storage tanks 2 Pump into the staining system.
[0075] (3) Turn on the heating and turn on the circulation pump at the same time. After the temperature rises to the temperature required for the deoiling process, use the extraction function of supercritical carbon dioxide to remove the oil on the polyester loose fiber. Turn on the separation and recovery unit to separate the oil agent from carbon dioxide and recover clean carbon dioxide. At the same time, turn on the low-temperature booster pump to pump new carbon dioxide into the system. ...
PUM
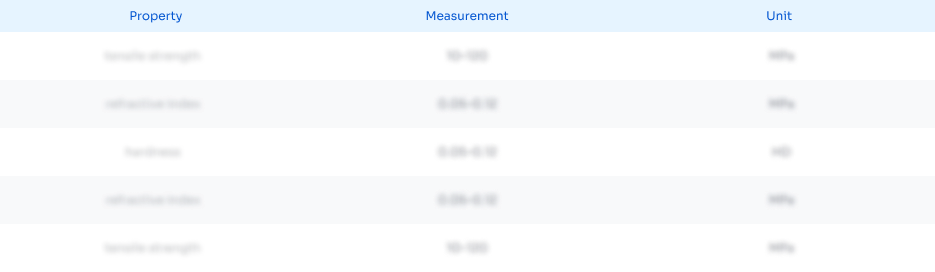
Abstract
Description
Claims
Application Information

- R&D Engineer
- R&D Manager
- IP Professional
- Industry Leading Data Capabilities
- Powerful AI technology
- Patent DNA Extraction
Browse by: Latest US Patents, China's latest patents, Technical Efficacy Thesaurus, Application Domain, Technology Topic, Popular Technical Reports.
© 2024 PatSnap. All rights reserved.Legal|Privacy policy|Modern Slavery Act Transparency Statement|Sitemap|About US| Contact US: help@patsnap.com