Thickened emulsion explosive and its manufacturing method
A technology of emulsified explosives and emulsifiers, which is applied in the direction of explosives, non-explosive/non-thermal agent components, non-explosive fillers/gelling agents/thickeners, etc., which can solve the complex production of mixed emulsion matrix, high charge pressure, Poor stability and other problems, to achieve the effect of improving explosive blasting performance, long storage period and good stability
- Summary
- Abstract
- Description
- Claims
- Application Information
AI Technical Summary
Problems solved by technology
Method used
Image
Examples
Embodiment 1
[0047] To prepare thickened emulsion explosives, follow the steps below:
[0048] (1) Prepare mixed emulsification matrix at the ground station: the weight content is 75.9wt% ammonium nitrate, 8wt% sodium nitrate, 0.1wt% acetic acid and 16wt% water are heated to 80 ℃, make water phase; Base oil and emulsification The agent is heated to 80°C to make an oil phase; the heated water phase and oil phase are mixed at a weight ratio of 94:6, and a mixed emulsification matrix is prepared through the ground pharmaceutical system. Here, the oil phase is obtained by mixing epoxidized soybean oil acrylate, machine oil and polyisobutylene succinate glycol amine emulsifier in a weight ratio of 1.5:2.5:2.
[0049] (2) Mix the mixed emulsifying base, sensitizer and thickener on the mixing truck: pass the mixed emulsifying base obtained in step (1) below 55°C with the sensitizer and amino terminal The butadiene-acrylonitrile liquid rubber is mixed and transported, and loaded into the blast ...
Embodiment 2
[0051] To prepare mixed emulsion explosives for thickening, follow the steps below:
[0052] (1) Preparation of mixed emulsification matrix at the ground station: heating 73.9wt% ammonium nitrate, 5wt% sodium nitrate, 5wt% calcium nitrate, 16wt% water and 0.1wt% acetic acid to 85° C. to make a water phase; Heat the base oil and emulsifier to 85°C to make an oil phase; mix the heated water phase and oil phase at a weight ratio of 94:6, and prepare a mixed emulsification matrix through the ground pharmaceutical system. Here, the oil phase is obtained by mixing corn oil, epoxidized soybean oil acrylate, synthetic oil and polyisobutylene triethanolamine succinate emulsifier in a weight ratio of 1.25:0.75:3:3.
[0053] (2) Mix the mixed emulsifying base, sensitizer and thickener on the mixing truck: pass the mixed emulsifying base obtained in step (1) below 55°C with the sensitizer and terminal hydroxyl Polybutadiene acrylonitrile is mixed and delivered, and loaded into the blast ...
Embodiment 3
[0055] To prepare mixed emulsion explosives for thickening, follow the steps below:
[0056] (1) Prepare mixed emulsification matrix at the ground station: the weight content is 73.85wt% ammonium nitrate, 10wt% sodium nitrate, 0.15wt% citric acid and 16wt% water are heated to 85 ℃, make water phase; Base oil and The emulsifier is heated to 75°C to form an oil phase; the heated water phase and oil phase are mixed at a weight ratio of 94:6, and a mixed emulsification matrix is prepared through the ground pharmaceutical system. Here, the oil phase is obtained by mixing soybean oil, motor oil and polyisobutylene succinate xylitol in a weight ratio of 2:2:2.
[0057] (2) Mix the mixed emulsifying base, sensitizer and thickener on the mixing truck: pass the mixed emulsifying base obtained in step (1) below 55°C with the sensitizer, amino terminal Liquid nitrile rubber and epoxidized soybean oil acrylate are mixed and delivered, and loaded into the blast hole to form a thickened e...
PUM
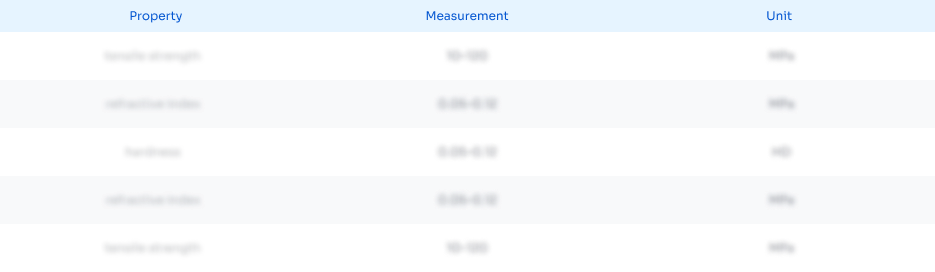
Abstract
Description
Claims
Application Information

- R&D Engineer
- R&D Manager
- IP Professional
- Industry Leading Data Capabilities
- Powerful AI technology
- Patent DNA Extraction
Browse by: Latest US Patents, China's latest patents, Technical Efficacy Thesaurus, Application Domain, Technology Topic, Popular Technical Reports.
© 2024 PatSnap. All rights reserved.Legal|Privacy policy|Modern Slavery Act Transparency Statement|Sitemap|About US| Contact US: help@patsnap.com